High-Temperature Anti-Seize Bearings, Bolts, and Bushings
Anti Seize Treatment against Galling, Corrosion and Wear Temperature Range: Liquid Nitrogen to 3000F?
Did you know that 30-60EJ of energy can be saved by reducing friction from 0.25 to 0.1 with the EION?
Metallic anti-seize GoldenBlue® provides superior protection against galling, corrosion, heat freeze, rust, and seizing on many metal surfaces. Use in oxidative conditions as well as reducing conditions. Smooth, hard, and high lubricity.
Read the article on nano-texture wear analysis
Read the article on self-organization during wear (see appendix)
The pulp and paper and food industry also use polymer-coated rollers and often make them anti-stick with polymer or cermets. The GoldenBlue&trade treatment could be a new coating technique to provide permanent low friction and heat and wear resistance. Typical treatment time would add one US cent per part for rollers and trays. Regardless this aspect should be tested on a case-by-case basis – which MHI will do free of cost while the program is offered. Imagine if soft coatings are replaced by the hard smooth wear-resistant GoldenBlue® at your own site with the Cascade e-Ion machines.
Possible uses – inside your plant – for: | Food, pharmaceutical, and drink industries also use non-stick in engineered parts and other surfaces like: |
---|---|
|
|
Wear resistance is generally improved with Galling resistance.
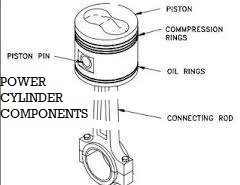
What are power cylinder components
Comparison of deposition methods 
In-situ Cascade e-Ion | Nano- 10 microns | Oxynitrides Nitrides Ti (C,O,N) Enhanced SiC and Ti(C,N,O) Si3N4 and variations | Galling and Wear Extreme Resistance Non Stick Corrosion Resistant Bearings and Anti Seize Anti friction Biomedical Cell Phones | Machine Tools Cast Iron Die Steel Stainless Steel Graphite Glass |
De-e-Ion Deposition | Nano-Microns- mm depends on objective. Cascade e-Ion assisted rapid deposition. | Alumina Molysilicides Carbides Diamond Coatings Composites | Anti microbial Dense and Hard Overlay Friction | Metals Polymers Ceramics |
PVD | 1 – 5 μm (40 – 200 μin) | Ti (C,N) | Wear resistance | Machine tools |
CVD | 1 – 50 μm (40 – 200 μin) | Sic | Wear resistance | Fiber coatings |
Baked polymers | 1 – 10 μm (40 – 400 μin) | Polymers | Corrosion resistance, aesthetics | Automobile |
Thermal spray | 0.04 – 3 mm (0.0015 – 0.12 in) | Ceramics and metallic alloys | Wear resistance, corrosion resistance | Bearings |
Hard chromium plate | 10 – 100 μm (40 – 200 μin) | Chrome | Wear resistance | Rolls |
Weld overlay | 0.5 – 5 mm (0.02 – 0.2 in) | Steel, stellite | Wear resistance | Valves |
Galvanize | 1 – 5 μm (40 – 200 μin) | Zinc | Corrosion resistance | Steel sheet |
Braze overlay | 10 – 100 μm (400 – 4000 μin) | Ni – Cr – B – Si alloys | Very hard, dense surface | Shafts |
Common Chemical compositions of some tool and die steels wt.% (nominal). H is hot work grade
Grade. | C | Mn | W | Si | Cr | Mo | V | Co |
W1 | 1.0 | 0.35 | 0.30 | – | – | – | – | – |
O1 | 0.95 | 1.1 | 0.5 | 0.30 | 0.5 | – | – | – |
A2 | 1.0 | 0.30 | – | 0.30 | 5.0 | 1.0 | – | – |
D2 | 1.55 | 0.30 | – | 0.30 | 12.0 | 1.0 | – | – |
S1 | 0.5 | 0.30 | 2.5 | 0.30 | 1.5 | – | – | – |
T15 | 1.6 | 0.30 | 12.0 | 0.30 | 4.0 | – | 5.0 | 5.0 |
M2 | 0.9 | 0.30 | 6.0 | 0.30 | 4.0 | 5.0 | 2.0 | – |
H13 | 0.35 | 0.40 | – | 1.0 | 5.0 | 1.5 | 1.0 | – |
P20 | 0.4 | 1.5 | – | 0.4 | 1.9 | 0.2 | – | – |
Picture shows Car Tappets and outlet valves GoldenBlue® by the Cascade eIon™ process for Low alloy medium carbon manganese containing steel.
Common Chemical compositions of some tool and die steels wt.% (nominal). H is hot work grade
Grade. | C | Mn | W | Si | Cr | Mo | V | Co |
W1 | 1.0 | 0.35 | 0.30 | – | – | – | – | – |
O1 | 0.95 | 1.1 | 0.5 | 0.30 | 0.5 | – | – | – |
A2 | 1.0 | 0.30 | – | 0.30 | 5.0 | 1.0 | – | – |
D2 | 1.55 | 0.30 | – | 0.30 | 12.0 | 1.0 | – | – |
S1 | 0.5 | 0.30 | 2.5 | 0.30 | 1.5 | – | – | – |
T15 | 1.6 | 0.30 | 12.0 | 0.30 | 4.0 | – | 5.0 | 5.0 |
M2 | 0.9 | 0.30 | 6.0 | 0.30 | 4.0 | 5.0 | 2.0 | – |
H13 | 0.35 | 0.40 | – | 1.0 | 5.0 | 1.5 | 1.0 | – |
P20 | 0.4 | 1.5 | – | 0.4 | 1.9 | 0.2 | – | – |
Brinell HB | Vickers Number, | Rockwell C |
. | 902/9020 | 65 |
. | 836/8360 | 63 |
. | 778/7780 | 61 |
601 | 715/7150 | 59 |
578 | 671/6170 | 57 |
534 | 599/5990 | 54 |
495 | 547/5470 | 50 |
477 | 523/5230 | 49 |
461 | 501/5010 | 48 |
444 | 479/4790 | 47 |
375 | 395/3950 | 40 |
363 | 382/3820 | 39 |
353 | 369/3690 | 37 |
341 | 356/3560 | 36 |
321 | 332/3320 | 33 |
262 | 267/2670 | 25 |
241 | 246/2460 | 21 |
235 | 240/2400 | 20 |
229 | 234/2340 | 99 Rockwell B |
223 | 228/2280 | 98 |
217 | 222/2220 | 97 |
212 | 217/2170 | 97 |
207 | 212/2120 | 96 |
201 | 206/2060 | 95 |
197 | 202/2020 | 94 |
192 | 197/1970 | 93 |
170 | 175/1750 | 87 |
Conversion Table for Hardness: Brinell, Vickers Number/Vickers MPa, Rockwell B and C.