Cascade e-Ion Devices
A Flame with Zero Carbon Emissions
Just immerse the part in the Cascade e-Ion plume for a few seconds. GoldenBlue®.
In the past, the costs associated with testing the myriad options for new technologies were extremely high. A perpetual battle exists between ideal engineering design and manufacturability on a production scale. Has the Cascade E-ion solved this?
Stable Thermal Cascade Plasma Generator. CleanElectricFlame®
The one technology that advances new mobility applications increases energy efficiency and reduces emissions.
Glass Bending, Optical Data Transfer, Biomedical Coating/ Deburr, Tool-bit Reconditioning, Abrasive Wheel, Cast-Iron, Stick Resistant Steel Surfaces, Anti-Seize Treatment for steel bearings, Bolts and bushing, Request Information
Compare with lasers, electron beams, and nitriding machines
Enhanced Corrosion resistance with significant hardness increase.
Uses for the Cascade eion A SmartPlasma Power Device | |
Create Easy, Non-Stick Surfaces for Cooking | Compare the Cost/Performance of NoScratch(TM) |
Data Glass Shaping | Communication Glass and Decorative Glass |
Biomedical | Titanium and Zirconium |
Rapid Brazing | Compare. 3DBrazing® |
Texture/Smoothing | Information Rapid deburring of threads and surfaces improved. |
Improved Machine Tool and Die Performance Easily deburr | Cool to machine – save $$$ |
Low Wear Surfaces (Automobiles) | Reduce friction. Reduce wear. High Nitrogen Content Alloy Carbonitriding or Austempering |
Save |
Special techniques for nanoporous surfaces for possible catalyst, solar, and antimicrobial use
with a modern open-plasma device.
4DSintering®.
High Hardness |
Use the SmartPlasma device. Compare with DLC and other Plasma methods. Create nanoscale Carbon Nitrides, Nitrogen Carbon, Borides, and Mixed Borides. Hard and Smooth Oxynitride Colors. High Vickers. Compound layers in steel form in situ or by graded layer processing. Use on chromium, molybdenum, manganese steels, titanium alloys, zirconium alloys, and diamonds. Oxynitrides are among the most important new materials for low-wear surfaces, plasmonics, solar cells, and glass coatings. The cascade e-ion beam enables Deburring. Create Non-stick surfaces for steel and cast iron or treat cell phone glass. The Cascade e-ion allows continuous, seamless processing for improved tool and die performance. Welcome to the world of two-dimensional materials formation of various types.
Microstructure, EDAX, and XPS results.
The Cascade e-ion processes allow continuous use. Traditional furnace-based batch treatment techniques could be expensive. Batch processes are often inefficient and costly due to high furnace and facilities costs. Compare processing time in seconds/minutes with long processing times in furnaces and the associated colossal energy consumption. Other expenses from batch coaters include frequent maintenance and repair with specialized labor. Extra steps like plasma cleaning or blanking parts may be required, which are mostly unnecessary with the Cascade e-Ion process. XPS and other delicate electronic probes display fine structure, depth of ionic penetration, and new phase formations, which are advantageously used.
The application of titanium, zirconium, iron, and steel alloys is limited by low shear strength, high coefficient of friction, low hardness, and poor wear resistance. The cascade e-ion is the first process to offer processing within seconds with no space limitations. Some of the ROIs are astounding. Some beneficial phases of iron nitrocarbides, carbonitride, smooth oxynitrides, compound phases/layers for hardness and high wear resistance, epsilon phases, and titania or other antimicrobial nanostructures may be experienced. Experience the possibilities of rapid bulk heat treating and quick brazing with meager operational costs – often less than a cent per part. Create conditions for chromium nitrides, titanium nitrides, tantalum, niobium and zirconium oxynitrides, manganese (oxy)nitrides, vanadium nitrides, oxycarbides, aluminides, aluminum/magnesium/silicon nitrides and oxynitrides (including composite combinations or particulate, fiber, functionally graded or grated layers). Lanthanum, perovskite Oxynitrides for photocatalytic power and photoconductivity. Ion nitride yittria zirconia films. Create functionally graded or grated layers with nanoscale oxynitrides, inorganic elements, and nitrides. Change the adherence in organic molecules by plasma polymerization on goggles, plastics, mold surfaces, and other parts by direct application. Combust coal and biomass to lessen the release of aromatics and complete combustion. Please contact MHI.
Case Studies have discussed that range from tool bit reconditioning to the accessible surface improvement of steels and cast irons. Bearings, axles, rails, deep-dishes, pans, broaches, carbide drills, cast irons, simple parts like nail clippers and scissors, complex parts that hold up space mirrors, and much more can be GoldenBlue® treated effortlessly with the cascade e-ion plume. Enjoy the benefit of high temperatures to create smooth and hard surfaces that are now made easy.
Choice of Plasma Plumes (choose any gas plus a circular, wide area or slot). Click on: What is Cascade e-ion? For information on the color of the plume and the color of the surfaces | |||
![]() | ![]() | ![]() | ![]() |
Is there a simple way to tell if the Cascade e-Ion Plume treated part is smoother? When nitrided or oxy-nitrided with the GoldenBlue® treatment, the swage-lock, high-temperature bolt, ball/roller bearing, or machine tool should make less noise when machining or putting on the nut. Less noise is an indicator of smoothness.
How is wear reduced? Material loss by tribological processes causes wear. The GoldenBlue® reduces galling, adhesion, abrasion, and tribo-oxidation depending on the alloy. See samples in the auto industry for rapid new techniques for austempering and martempering.
Figures show Cascade e-Ion Machines. Permanently color your hard surface.
Bring your designs to life with beautiful colors and improved engineering surfaces.
Simplified Surface Engineering Processing: Immerse in the Cascade e-Ion Plume
Information
What is a Cascade e-ion?
Selection Guide and Comparison
Models https://mhi-inc.com/cascade-e-ion-plasma-models/
Industrial Applications https://mhi-inc.com/industrial-applications-of-cascade-e-ion-machine-stations/
Compare with Lasers, Electron Beams, and Sunlight https://mhi-inc.com/cascade-e-ion-vs-lasers/
Clean ElectricFlame Technology https://mhi-inc.com/cleanelectricflame-technology/
What can the Cascade e-Ion CleanElectricFlame™
do for your industry?
It is one of the most novel surface enhancements available today.
Improve Process and Process Energy and Productivity, sometimes by over 50%.
Improved Material ( Higher hardness, better wear, drop friction by over 50%).
Eliminate carbon and eliminate carbon-containing lubrication.
Bend Data Glass.
Easy Deburr
Keep fluid nozzles smooth and clean.
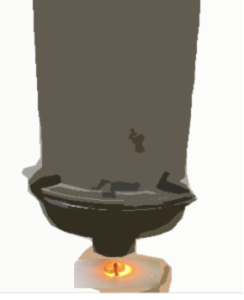
Eion in use (smallest size ~6 kW)
The Cascade CleanElectricFlame® technology uses just electricity and air (or other gasses if required, like Nitrogen, Argon, or Forming Gas) leaving behind no residues. MHI’s Cascade e-Ion Plasma™ uses less energy, produces hardly any noise, and is safer than traditional heating methods. It is one of the most special plumes available. The Cascade e-Ion systems are available for use with hard alloys, plastics, metals, glass forming, ceramics, composites, and several other materials – even food or wood. The Cascade e-Ion devices can be used for sintering, for example, titanium and carbon mixed powders in minutes. Large surface plates are easily moved under the beam. The CleanElectricFlame® provides a Cascade e-Ion environment.
The Cascade e-Ion can bend, nitride, create surface borides like Zirconium diboride and alloys, and for inducing colorful smooth surface oxynitride of many materials including manganese, chromium, titanium, copper/ graphite, and glass.
A possible use for automotive axles, pistons, tappets, piston rings, valve stems, guides crankshafts with quick low-cost nitriding(O) – even for space re-entry surfacing. The CleanElectricFlame® provides a new type of reducing environment. Even difficult materials like copper and tungsten-copper alloys have a shiny finish after the Cascade e-Ion plume treatment. In situ growth of nitrides and oxynitrides is a special “open” feature that only the plume from the Cascade e-ion can accomplish. Adopt early. Early-stage pricing and possible MHI partner financing are available. MHI offers an attractive MHI-Never-Down program. Please ask for details on the Cascade e-Ion Models, like the unique MHI-Never-Down program warranty-type features and, if required, MHI Financing. Click on the left navigation bar “solutions” to view several of the case studies.
Contact MHI for tool energy savings and astounding ROI possibilities for engine valve steels like EN grades, 21-4N, 52000, and others.
For Cascade e-Ion
– Heat up rate 100K/s (Kelvin per second). Ionic heat transfer.
– Price per part for several small parts using only air and electric ~ 0.2US¢/part.
Price of Energy: The price of energy depends on the source but is not that different between different forms of energy that one can use (e.g. gas or electric). Comparisons are given for example on Duke Energy. In the US, when comparing gas and electric a rule of thumb is that gas energy is about 75% lower cost when compared with the same quantity of electric energy. However electric machines are generally much more efficient than gas heaters. For example, the OAB or Cascade e-ion can save you even 90% of traditional energy use in relevant applications. These new machines can dramatically influence operational costs. Often using electric heating is less polluting at the use point. Additionally, electric heaters can be efficiently/accurately controlled. Both KWhr and Therm are units of energy.
1kJ (KiloJoule) = 0.9485 BTU=0.0002778 kWhr. One Million BTU (MBTU) = 10.002 Therm (US). Electric energy is normally priced for every KWhr used, while gas is priced by the number of Therms used.
Source: MHI Energy efficiency
- Customize for deposition type and shape. Contact MHI.
- Compare price and energy efficiency with ordinarily transferred arc, induction plasma deposition, or laser.
There are no electrodes to change in cascade plasmas. - Improve Surfaces from Tool bits, Non-stick to Electrical. Titanium Oxynitride-Nitride, Yittria Zirconia (with dopants), Boron Carbide, Silicon Carbide, and Molybdenum disilicide.
- Super-ionic bending and Ionic Surface Hardened Glass and Nano Surface Depositions.
- WC and other high wear-resistant surfaces for tool bits.
- Tubes and complex shapes. Thick Alumina on Aluminum. In situ nitriding of tubes for dies.
- Easily make functionally graded coatings.
- Custom Turnkey Solutions with Complete Electronic Controls. Increase endurance of stamping and hot working dies,
- Highly stable e-Ion cascade thermal plasma™
- New ionic low-cost surface treating and deposition. Minimize pollution and minimize noise – improve energy efficiency.
- Titanium Oxynitride Nitride coatings on HSS and other surfaces. Easy oxynitride or nitride formers are Ti, V, Zr, Al, Mn, Mo, Fr, Cr, and many others. In addition, various eta phases of carbon nitrides and borides are possible.
- Non-stick, high-hardness metallic surfaces
- MHI provides a coating for Nickel Aluminide formation with the cascade e ion. Contact MHI.
Petrochemical: reforming furnaces, cracking furnaces, pyrolysis and fired heaters,
- Clean aluminum production.
- Clean Coal Combustion and Ignition (reduced aromatics).
- VOC cleaning.
- Glass-making industry: Roll barrels for float glass line
- Color of surfaces. Contact MHI for Edax, Microstructure, and XPS results where available.
- Aircraft and automobile engine parts
- Printing on plastic food containers
- Energy-efficient window coatings
- Safe drinking water
- Voice and data communications components
- Waste processing
- Coatings and films
- Electronic computer chips and integrated circuits
- Advanced materials (e.g., ceramics)
- High-efficiency lighting
- Plasma enhanced chemistry
- Surface cleaning
- Processing of plastics
- Gas treatment
- Spraying of materials
- Chemical analysis
- Semiconductor production for computers
- TVs and electronics
- Sterilization of medical tools
From surface crystal growth technology to surface nitriding, the Cascade e-Ion places the technical process and value-addition possibilities squarely in the hands of innovators of tool-bits, steel parts, cast iron, and steel manufacturers primary and secondary non-stick-surface manufacturers, solar cell materials and shapes, hydrogen storage, and wafer manufacturers – thus giving everyone new market opportunities. The Cascade e-Ion makes providing dross-reducing covers for melting metals extremely feasible. The DRO models are particularly well-designed for this type of solution. The cascade e-ion can make magnets better for corrosion resistance or high-temperature oxidation. How do you know that the surface is harder? Bounce the ball bearing and watch if it bounces higher than the non-coated bearing.
Learn More About Cascade e-Ion Plasma™ Technology.
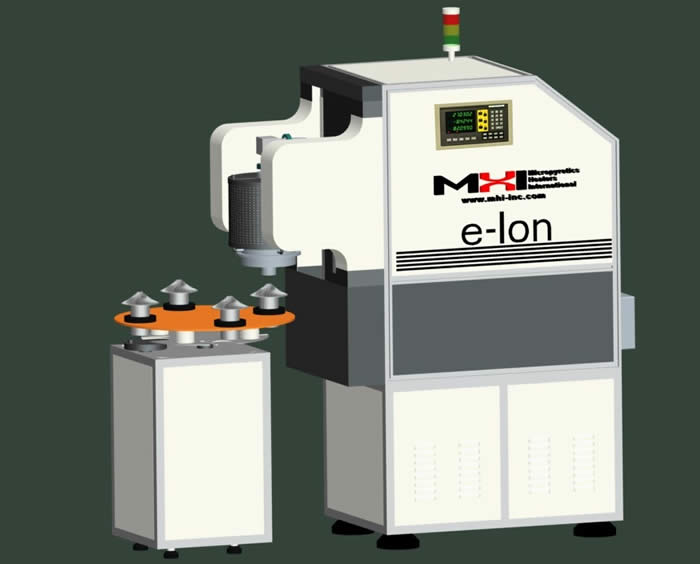
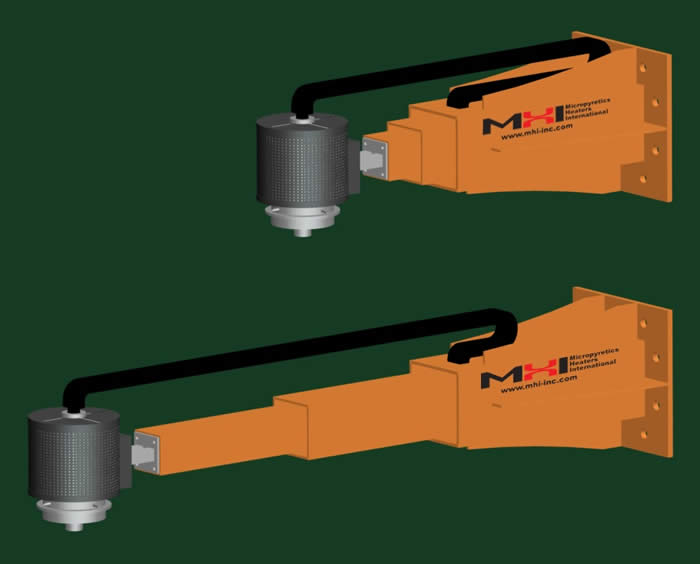
What is Cascade e-Ion Plasma™ | Extremely Wide Area Plasma (with LIP) | Extremely Rapid Depositor De-e-Ion Models with arrangements possible for trials on surface reconditioning with purchased units?
- Save energy: use ~15kW, not ~150kW. In dollars? Please click here.
- Air is used as input gas for almost all applications because of the heavy nitrogen ions in the plume.
- Accessible port for steam and any other gases.
- If using other gas, switch to air when not in use.
- Use time is short. Grow unusual smooth surfaces within seconds.
- Enjoy the flexibility of operation (just immerse or impinge plume on part).
- Reasonable control over the depth of the “white layer” so that finish lapping is not required.
- Particularly suitable for large or small-batch production.
- Large or heavy components of conventional plasma that normally cannot be treated (because of a lack of process control) can now be economically nitrioxynitridedride.
- Deburr.
- Enjoy MHI-Never-Down Program.
- Quick installation and use.
- Best of MHI Sales and Service.
- 3DBrazing and 4DSintering®are registered trademarks of MHI.
Contact Us for a Demonstration
We may not yet have all the answers on every application, so we may not be sure if the Cascade e-Ion Plasma™ is always right for you. However, for most surfaces, the CleanElectricFlame™ provides the best plasma, ion-implantation, and modified chemical species, enough to warrant a trial (payment may be required) on your part. Regardless of whether we know what the treatment offers for a specific untested surface, we can certainly arrange to have your part treated during a live video conference. Contact MHI. It is worth a try!
Improved Energy Efficiency From:
a) When the part or tool lasts longer or can be used at higher speeds.
b) The tool requires a lesser number of replacements.
c) When dry machining is possible. Dry machining has great potential for improved energy and resource efficiency.
d) Manufacturing tools are the lowest energy procedure, so the total energy cycle is minimal. (e.g.as with the Cascade e-Ion).
Please compare GoldenBlue® to other tools/drills and bits.