Steam Solutions Comparison
What is the difference between an industrial (pressure) boiler and an electric steam generator?
An electric steam generator can be almost 50% more efficient in energy use than a fossil fuel steam generator. (approximate comparison only – please get in touch with MHI for details and assumptions used – Note 1 BHP~9.6KW)
Boilers are slow for steam production compared to steam generators. Boilers create steam by boiling water in a heated pressure vessel; the pressure builds up to the required saturation temperature for steam generation. In a typical boiler, the steam generation occurs at the imposed pressure – this type of steam is called saturated steam. Saturated or boiler steam may be wet and contain water droplets. Boilers require high pressure to get to high temperatures; e.g., 200°C requires 225 psi (15.5 Bar) pressure capability. Even at 100 Bars, the saturation temperature is only 311°C. Traditional pressure boilers make saturated steam that can sometimes be mildly superheated. Boilers represent older steam technology (see Chronology of steam production).
On the other hand, electric steam generators are modern rapid steam production devices with instant on-off features, steam velocity control features, independent backpressure control, and significant high-temperature steam capability with dry steam (without needing pressure vessels or pressure unless required for the backpressure). MHI electric steam generators do not have to operate at high pressure to obtain high temperatures. Temperatures of ~1000°C can be obtained with no high-pressure vessel requirement.
Click for Electric Steam Generator Models.
A comparison for 400 Kg/hr steam made by natural-gas combustion energy and electric energy.
Natural Gas Steam Generator/Pressure Boiler: The power and corresponding energy can be as high as ~75BHP (fuel) with fossil fuel sources. The temperature of the steam is low, and the steam is wet, typically saturated (100°C at 1 Atmosphere) with almost 5% water. Requires exhaust stack. Requires blowdown.
Electric Steam Generator: The power and corresponding energy used is ~35BHP (electric)—very dry steam. Steam temperature can be 300C or above with no pressure build-up unless required—no water vapor. No exhaust system is required. Avoids blowdown. Water can be recycled.
When to choose a clean electric steam generator:
- The required temperature is above the saturation temperature. For example it is >110°C (~230°F) for 1 atmosphere back pressure requirement,
- High-quality steam is required,
- A variable flow rate may be necessary,
- Adjustable temperature, high energy efficiency, and a small footprint are desirable,
- Modern touchscreen controls and data management are helpful,
- Decarbonization is essential. CO2 and Nox generation must be avoided.
- Recycling water with minimum conditioning is necessary (say, on an ocean platform).
- Easy installation and easy use are required.
- When compactness is desired.
Because of its energy efficiency, controllability, and on-off features without idling, a steam generator may be the most economical choice e. (Scroll below for more comparisons). Steam generators are constructed with water monitoring and low blowdown requirements.
Click for Steam Generator Models. (Typical only – please get in touch with MHI for details and assumptions used – Note 1 BHP~9.6KW)
Steam Generators can operate at room pressure or at the backpressure required to be overcome to yield the needed temperature of 150°C, 200°C, 300°C, 400°C, 500°C, 600°C, 700°C, 800°C, and even up to 1300 C. With steam generators, one can get high temperatures in the steam gas without using unwieldy pressures.
Compare pressure boilers and steam generators.
- Temperature Limitations – Industrial boilers require high pressures for higher temperatures. Not so for steam generators.
- Boilers typically sacrifice efficiency or safety to operate at lower temperatures than rated. Not so for the steam generator. As a boiler’s pressure rating increases, its efficiency often falls.
- Combustion Process—Nearly all large-scale industrial boilers utilize the combustion process. Combustion fuels CO2 and NOX production and fossil fuel consumption. Combustion processes typically result in low efficiencies and high energy losses, especially with increasing pressure.
- Safety—Pressure vessels can fail and explode (although this is rare as many boilermakers follow best practices with safety relief ). Low water levels can result in boiler overheating and potentially lead to an explosion. Gas leaks pose an inhalation danger as well as an explosion risk.
- Certifications—Any boiler or pressure vessel requires certificates and inspection. However, open-flow steam generators may not require unique and yearly credentials based on several criteria. Review the boiler regulations for your state. Rules are typical in Canada.
- Traditional pressure boilers require a blowdown. Modern steam generators avoid costly downtime or added equipment.
- Difficult to Use Boilers – Boiler operation typically depends on specific, trained individuals trained to read dials and follow numerous safety measures per local code. Boilers are complicated.
Steam Generators use 21st-century technology—no combustion or pressure vessels. The OAB and HGA patented technologies allow steam generators to operate with unparalleled efficiencies, saving you time and money and improving your process. Industrial boilers have worked well in the past, but they are 19th- and 20th-century technology machines with low efficiencies. They can reach 85% efficiency in many configurations (only at a steady state, which often takes longer for boilers), and they still have significant drawbacks in temperature capability. As the pressure rating increases, the efficiency of boilers often falls. Steam generators, like the OAB or HGA type, routinely offer over 95% efficiency even to 800°C and beyond (a temperature unimaginable for boiler-made steam).
Table of Comparison
Feature | OAB® Steam or MightySteam | Water Tube Steam Boilers, Non-Electric | Electric High-Pressure Steam Boilers |
Maximum Steam Temperature1 Always Clean Steam? | 120-1300°C Standard. Choice of Models. Consistently high flow. No moisture. High performance. Yes | Mainly 120 C., sometimes up to 600°C with an Economizer and Superheater. Boilers take a long time to achieve a steady state. No | 134°C for 3 Bar steam. No |
Delivery to Initial Startup. How Versatile | Models are easily installed in a day, and there is no anticipated wait for certifications to start. Independent temperature, flow, and pressure settings | Unknown Not all types are versatile or compact. | Small units could be plug-and-play. Large units may require certification time. Generally not versatile. |
Efficiency | >90-98%. Instant Steam. | <70-90% (at steady state, much lower otherwise) | ~85-95% (at steady state, much lower otherwise) |
Idle Energy Waste | None (Choice of Continuous or On-off Steady-state steam) | High | Moderate |
Steam Production Usage Time (Startup Time2) | Start and Stop. Nearly Instant. Generally, within a minute. | 60+ Minutes. Becomes slower with higher pressures and volume requirements | ~60 Minutes. Becomes slower with higher pressures and volumes. (Time does not include cool down and pressure release durations for autoclaves) |
Suggested Inlet Temperature/Pressure3 | Tap/Tap PressureRO-type water | 40-60 F. Water has to be conditioned. | 20-35 C. Water has to be conditioned. |
Capital Cost per Kg of Steam3 | Medium. Financing is available when qualified. | High | Moderate. Depends on the temperature/pressure required. |
Operational Costs4 | Low even up to 1300°C. Modern HMI and PLC control—touch screen operation. | High | Low-Moderate |
Unit Footprint | Starting at 1’x 1’x 1′, depending on the steam rate required. A typical 180 KW unit is 4ft x 4 ft. Small and remotely locatable power panels. | Large | Depends on size and pressure requirements. |
Plug & Play Operations | Yes | No | No |
Requires Boiler Certifications5 Review the boiler regulations for your state. Canada. | Generally, no, but it could vary for different generators. | Yes | Yes |
Downtime6 | Low (Unit can be used for continuous steady-state steam ). Because of the low footprint and modular designs, the MHI-Never-Down Service™ is available for all steam units. Self Draining Self Flushing | Low-Moderate It may require complex flushing and draining operations. | Low It may require complex flushing and draining operations. |
Utilizes Combustion Heat 7 (Requires Ventilation) Combustion creates CO2 and NOx | No | Yes. High social costs of CO2 and NOx are made. In the future, there is a likelihood of carbon taxes. | No |
Energy Needed to produce 100 Kg/hr steam from a cold start | ~70 kWh for steam @~200 C. Water at Room Temperature to Steam. | ~150-200 kWh Equivalent (Including startup time consumption). Not always reported from room temperature water. | ~150kWh Equivalent (Including startup time consumption). Not always reported from room temperature water. |
Power Weight [Kg Equipment/(Kg/hr) of steam] for a 100kW Generator | ~2 Kg per Kg/hr of ste m. Variable. | ~5 Kg/hr of steam (Weight increases with temperature/pressure). Variable | |
Maximum Work Potential (Based on second law limitation) Base is 1 Bar 100C liquid water for all. | 672 kJ/Kg for 500°C superheated steam 1973 kJ/Kg for 1300°C superheated steam | 755 kJ/Kg for 10 Bar saturated steam 1169 kJ/Kg at 100 Bar saturated steam. | Generally not used for creating work. |
Enthalpy (heat) Content | 3489 kJ/Kg for 500°C superheated steam at 1 Bar | 2777 kJ/Kg for 10 Bar saturated steam Saturation steam temperature 180°C | 2725 kJ/Kg for 3 Bar saturated steam Saturation steam temperature 134°C |
Running at Partial Capacity | With MHI Electronic Controls, there is no significant loss of efficiency. | Significantly lower efficiencies, even if the model is capable | Lower efficiencies |
Air Contamination Effects | Extremely high operation temperatures diminish the effects of contaminated air, if any. | Air contamination harms the output | No air contamination is allowed (strict) |
Piping Losses | Discrete, locatable units reduce necessary piping. The one-atmosphere pipe can be better insulated and lighter. | High pipeline pressure combined with long piping distances leads to heat loss and dangerous conditions in the event of pipe failure. Pipes can be heavy. | High pipeline pressure combined with long piping distances leads to heat loss and dangerous conditions in the event of pipe failure. Pipes can be heavy. |
How far can I run my pipe? Infographic. | Low piping losses. Variable. | Unknown. | Unknown. |
Typical Improved Efficiencies (Energy) | Application dependent – sometimes over 50% improvement over combustion. | ||
Improved Water Efficiency | Application dependent – sometimes over 50% improvement over combustion. | Not very efficient | Moderate efficiency |
![]() |
Steam Without the Wait. Compare Electric Steam Generated Steam with Fossil Fuel Generated Steam.
- Generally, electric steam generators are far more efficient than fossil fuel Systems (nothing to exhaust). In electric systems, there are electric boilers and instant electric steam generators.
- A 9 MW fossil fuel boiler, will make ~1.6 – 5 tons per hour of CO2 equivalent GHG (please click on https://mhi-inc.com/decarbonization-project-costing-analysis-energy-efficiency/). The cost of making a ton of CO2 equivalence (i.e., the climate-toxic emissions of CO2, Methane, SO2, Nox, and Soot) is hundreds of dollars. (Source US Government and https://en.wikipedia.org/wiki/Social_cost_of_carbon)
- Some steam systems (especially 5MW and higher) are offered at 4160V. It is called Medium Volts but is a hazardous high voltage requiring some trained personnel. However, the Electric panel of a 4160V system could be smaller than a 480V panel. Please check with electrical engineers about potential hazards and how to prevent them.
- The steam temperature should be greater than 180C -200C -dry steam for rapid noncondensing antimicrobial action. The temperature is important- previously unavailable from boilers. Electric Steam Generators can do this easily, but it is a colossal struggle for fossil-fueled boilers. It would help if your steam were above the inversion temperature (see the MHI website for published scholarly articles for drying and antimicrobial steam). Good dry steam considerably reduces the use time in many applications and prevents condensation. Condensation is a significant drain on efficiency. Today, no one uses simple utility steam as it is preferable to always have dry steam for everything. (See very large site https://bayzi.com/learning-center-for-high-quality-steam-and-humidity-for-sanitation-of-materials/)
- Finally, electric steam generators can be used at distributed sites as they are small and have no emissions. Instant steam generation is available today, and most people are moving to distributed systems, say ~1- 3MW each. It saves gobbles of energy, as one can imagine.
- Electric steam generators also offer new features for customers to control their processes – like variable flow, variable temperatures, automatic process triggers, instant steam generation, and on and off at will. https://mhi-inc.com/when-you-need-superheated-steam/
MHI has an energy-efficient, high-productivity solution for your steam application with new steam technology for high-quality steam. The BoilerFreeTM technology allows nearly instant steam production. Most MHI steam generators produce super-heated in under a minute from a cold start (it can take a boiler many hours or days). Please contact MHI.
Modern Steam Sensors Work Hard For You. Did you know that the steam generator units constantly monitor the incoming electric phases for any imbalance, allow variable water flow, keep an eye on the quality of the water in the reservoir, display steam temperature, and much more?
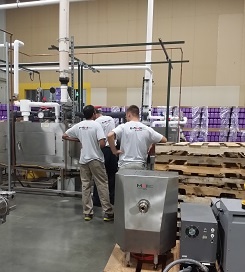
OAB installation for packaging steam tunnels.
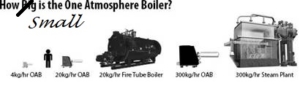
Compare the footprint of boilers and steam generators.
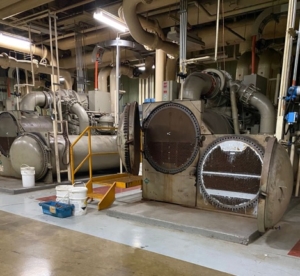
Old-style Boilers are massive and constantly under repair. It is better to change to an OAB steam generator.
Want to find out how MHI can help you meet your steam needs?
Please fill out a quick questionnaire by clicking on the product of interest.
We will help find a good solution to meet your needs.