High Energy Efficiency, Zero Emissions, and Improved Process Uniformity with the Airtorch® and MightySteam® – Project Analysis for Deep Decarbonization – Solutions for Better Process Performance and Cost Savings Using Efficient Heaters.
Summary: Both energy efficiency and productivity dramatically influence the payback period and overall returns for any expenditure. Productivity (i.e.., parts produced per unit time) is known to increase with uniformity and higher temperature of processing. Energy efficiency is a vital measure of how we utilize energy. Although all types of energy prices are high and climbing, it is best to use electric energy because the efficiencies of electric heaters are very high compared to fossil fuel heaters ( primarily, there are no flue gas or other losses with electric-powered process heat or steam generation systems).
“How” we use energy is as important as “how” we produce electrical energy. Products featuring advanced automated electric heating solutions, such as the Airtorch®, MightySteam®, E-Ion®, and Large Radiative Panels, enhance energy efficiency, operational performance, and uniformity, thereby significantly boosting productivity. The current volatility in climate and weather events is expected to decrease as the Earth’s warming rate slows down when emissions are reduced through energy-efficient industrial heating electrification. MHI Inc. recognizes that electrifying industrial heating systems presents a key opportunity to achieve significant energy savings and deep decarbonization for zero emissions. The focus on decarbonization effectiveness must consider not only how we produce electrical energy but also how we use it. In today’s rapidly changing industrial landscape, the urgent need for decarbonization and sustainability has become a central focus for businesses worldwide.
Any reduction in greenhouse gas (GHG) emissions is beneficial. Industrial Choices.
The gamut of decarbonization products across a range of application temperatures.
As climate change accelerates and weather patterns become more unpredictable, it is becoming increasingly important for industries to shift away from fossil fuel-based systems. Electric heaters offer a significant return on investment, boasting approximately 95% energy efficiency compared to traditional fossil fuel options, which range from 35% to 83% efficiency depending on factors such as flue loss, combustion efficiency, and overall thermal efficiency. This transition reduces greenhouse gas emissions and decreases the overall asset loss costs associated with carbon emissions. Although some changes are taking place in regulation, new regulations, such as the SEC’s climate disclosure rules, require companies to assess and report climate-related risks, driving the need for transparent environmental strategies. By adopting high-efficiency electric heating technologies, MHI Inc. empowers its customers to improve their Environmental, Social, and Governance (ESG) metrics while meeting these new requirements.
Energy efficiency programs, even those using software solutions, often cannot be integrated into existing operations because fossil fuel heaters have technical limitations. However, new electric technologies and rapid payback can reduce energy costs with better control while dramatically increasing efficiency.
The pursuit of decarbonization is not only an environmental necessity but also a fundamental aspect of modern industrial practices. It offers a promising balance of profitability and sustainability for the future, with payback periods ranging from one to four years and a high payback rate, even when emissions costs are not included (for details on the assumptions used in the calculations, please contact MHI). When emissions costs are considered, the payback period is correspondingly considerably shorter. This webpage provides several examples of electric heating methods with high overall efficiencies.
Please contact us for details and assumptions for the calculations for your specific installation.
Emissions Saved by Converting to Electrical Heaters: (4.17-6.99) × 10-4 metric tons of CO2/kWh (source).
CO2 Emissions Equivalence of GHGs: 1 kg of nitrous oxides (includes NO, NO2, N2O, and others) and 1 kg of methane emissions are equivalent to 298 kg and 25 kg, respectively, of CO2 emissions.
- The five major key greenhouse gases are carbon dioxide, nitrous oxide(s), methane, chlorofluorocarbons, and water vapor.
Excess Electric Power: The United States has 63 GW of capacity above and beyond the NERC target reserve supply 2013. Source. In 2023, capacity additions (35,807 MW) outpaced retirements (15,722 MW). about 65% of the capacity retired was from coal-fired facilities. Source.
Climate change refers to long-term temperature shifts and changes in erratic weather patterns. Its consequences include intense droughts, water scarcity, severe wildfires, rising sea levels, flooding, melting polar ice, catastrophic storms, and declining biodiversity. Climate warming is primarily caused by the burning of fossil fuels, which produce greenhouse gases (GHGs) such as carbon dioxide (CO2), several nitrogen oxides (clubbed as NOx), sulfur dioxide (SO2), and soot. These either absorb or react to absorb IR and near-IR radiation, thus trapping heat along with cloud formations. The increase in the average temperature and humidity in the immediate atmosphere, called the troposphere, leads to severe weather events that result in significant global asset losses. Focused spots of extreme heat waves and stormy weather are now emerging globally as a unwelcome weather pattern. As the tropospheric instabilities continue to manifest, it is not clear how these extreme-weather regions will behave. Climate predictability has worsened, as predicted by the increasing rate of tropospheric entropy generation.
The emissions of carbon dioxide (CO2) and other greenhouse gases (GHGs) carry a significant social cost. For example, 1 kilogram of nitrous oxide (N2O NO, NO2, and others) is equivalent to 298 kilograms of CO2 for global warming purposes. Similarly, 1 kilogram of methane (CH4) equals 25 kilograms of CO2. Among the key sectors contributing to CO2 emissions—transportation, power generation, and industrial heating—electrifying industrial heating presents one of the lowest costs per kilowatt, making it an effective strategy for reducing global emissions. Thus, eliminating fossil fuel combustion is a critical priority. The global asset losses associated with every kilogram of CO2 emissions can range from $51 to $3,000 per ton (the average was recently about $283 per ton of CO2 as per PNAS in 2024).
We only have to replace a third of the primary energy we use today to maintain our lifestyle and economy. Source
A 1 MW electric conversion can save over 250 to 600 kg/h of CO2. Efforts are underway to capture CO2, but this could be expensive. The costs of capturing and storing CO2 vary widely, from about $20 to $120 per ton, while direct air capture (DAC) can exceed $400 per ton. Direct capture methods are very energy-intensive –Source. Therefore, investing in high-efficiency equipment that minimizes GHG emissions is a sensible approach. (Source).
On December 2, 2023, the US Environmental Protection Agency (EPA) released a report increasing estimates of the social cost of greenhouse gases. This is further underscored by the new climate disclosure rules introduced by the Securities and Exchange Commission (SEC) on March 6, 2024, requiring companies to disclose climate-related risks that may impact their business. New climate fines and taxes based on the amount of greenhouse gases released into the atmosphere will be paid into Climate Superfunds [source]. Such fines are direct outlays in project costs, which are discussed below.
MHI Inc. has identified transitioning to electric heating as the fastest route to global decarbonization while providing clients with reliable ESG impact assessments. These regulatory changes reflect a growing demand for transparency in ESG matters. While around 50% of Fortune 500 companies have climate plans, all large, medium, and small companies must rapidly convert to electric heating systems. Electrifying industrial heating offers one of the most effective strategies to lower global emissions.
Go Electric with the Airtorch®, MightySteam®, E-Ion, and Large Radiative Panels.
Fossil fuels are in the news- but not in a good way. The hottest year on record was 2023, and 2024 is set to break this record. January 2025 was the hottest January on record. In May 2024, carbon dioxide levels measured at NOAA’s observatory peaked at 424 parts per million. 2024 had the highest rate of growth in emissions. For the first time, the global average temperature in late 2023 was more than 2 Celsius warmer than levels before industrialization, according to preliminary data (source citation). New mandates for decarbonization, such as the one for Federal buildings, are being considered the world over. Click here for per-capita and country-wide GHG emissions. Industrial, home, and rental repair incidence has been notably climbing.
Industry Is the Fastest Growing Source of Greenhouse Gas Emissions
Since 1990, the four emissions sources that have grown the fastest are industrial processes, which grew by a massive 225%; electricity and heating (a subsector of energy), which grew by 88%; transportation (also a subsector of energy), which grew by 66%; and manufacturing and construction, which grew by 60%. (Source) Sea temperatures and Land temperatures are both rising rapidly. The primary source of CO2 accumulation in the troposphere is the burning of fossil fuels.
Fossil fuels, such as coal, natural gas, and oil, are nonrenewable energy sources that produce CO2 and other greenhouse gases when burned. Burning such fuel is a significant contributor to planet-warming pollution in our atmosphere.
- The widespread use of fossil fuels also magnifies energy inefficiency. In 2019, of the 600 EJ (Exajoules) of energy produced, only ~200 EJ was used productively. The rest, almost 400 EJ, was wasted.
- Sometimes, waste is inevitable, and a balance has to be struck. For example, traction is impossible without some friction, but friction also causes energy loss because it produces heat. Considerable global research goes into reducing friction or finding the right balance between helpful friction and friction-related energy and material losses. For example, the special plasma treatment of drills can make them suitable for green machining criteria.
- But sometimes one can and should prevent loss – e.g., from smokestacks (a necessary feature of fossil fuel burning is the energy loss from combustion gases).
- Particulates called aerosols are also emission products that impact global heating and cooling. Aerosols can influence the Earth’s climate in two ways. When the sky is clear (devoid of clouds), reflective aerosols can reflect incoming sunlight to outer space. This blocks part of the energy that would have reached the surface, thus cooling the climate. However, absorbing aerosols, notably black carbon (fine soot), can trap solar energy within the atmosphere. The enhanced atmospheric heating eventually warms up the troposphere and the Earth’s surface and counteracts any cooling caused by reflection. At this time, the effect of aerosols is not entirely understood, but experimental evidence exists for positive global warming rates.
- Climate sensitivity is measured by the change in temperature expected when the tropospheric CO2 changes. This sensitivity has been increasing. Fossil fuel combustion, which currently adds about two ppm of CO2 to the troposphere annually, is the leading cause of an unstable atmosphere. An increasing tropospheric entropy density rate occurs with an increasing rate of the tropospheric CO2 and temperature (10−8 J/(m3.K.s.ppm(CO2) Citation. The rising entropy generation rate triggers erratic and intense weather. A video that relates global warming to climate change is shown here.
In 2023, wildfires in Hawaii claimed 97 lives, while blazes in Canada blanketed much of the Eastern US with smoke for weeks. The Florida Keys soared to 101.19F (38.43C) in December 2023, which could be a global record as ocean heat reaches unprecedented extremes. Developing an actionable, fact-based, and implementation-ready plan that effectively balances and prioritizes the components of deep decarbonization, namely Electrification, operational efficiency, clean fuels, and smart sourcing, can be a competitive advantage.. Using high-efficiency electrical, industrial heating is not only climate-friendly but brings about (1) a significant lowering of energy use, (2) enables downstream process efficiencies, (3) enhances safety, (4) allows efficient grid stability from renewables, and (5) mitigates climate-related health problems associated with fossil fuel usage. Contact MHI for project payback metrics.
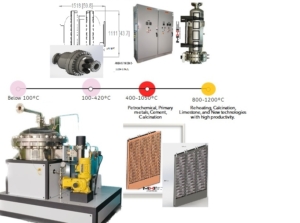
MHI offers a Range of Decarbonization and Load Reduction Electric Heating Products for Steel, Cement, Food and Beverages, Drying, Heat treating, Glass, Batteries, and Chemicals.
There is a push towards renewable power. Renewable power is both cost-competitive and the most cost-effective energy source in many situations, depending on the location and season. Such resources (also called low-exergy fuels) are finite in quantity and can take hundreds of thousands of years to form, and whereafter, they must be extracted from the Earth and burned to create energy. In 2023, about 60% of US utility-scale electricity generation was produced from fossil fuels (coal, natural gas, and petroleum), about 19% was from nuclear energy, and about 21% was from renewable energy sources. Source.
High-efficiency electric devices reduce the grid’s load. Newer electric technologies, such as efficient Airtorch or instant MightySteam and thermal batteries (LDES), improve grid stability and permit clean energy processes. Dirty energy sources, including coal, gas, and oil, are nonrenewable.
Deep decarbonization eliminates CO2 and other greenhouse gas emissions (GHG) from any process, making it a crucial sustainability advantage.
Sustainability initiatives can help improve financial performance with high public support as these initiatives have a global impact. Companies with a high sustainability vision tend to have a lower cost of debt and appear to have better operations management. Sustainability includes:
- Climate risk management with the elimination of fossil fuel use.
- Electrification, energy, and emissions reduction.
- Company-wide sustainability strategies.
- Resilient infrastructure with intelligent operations.
- Sustainable supply chains.
The deep decarbonization market for industrial heating is expected to top US $1 trillion and aid global health. When transitioning to electrical systems, using technologies that offer the highest efficiency (>96%) is essential. Modern controls, optimized materials, and design are critical selection criteria for this global effort.
Equipment for deep decarbonization
High-efficiency electric industrial heating systems, including steam or energy-efficient convective heaters, are now available for electrifying industrial heating systems with zero CO2, NOx, and SO2 emissions. Deep decarbonization is a competitive advantage. Electric systems offer many advantages in control and improved productivity in industrial furnace processes, drying and roasting, cement, steel, aluminum, magnesium, comfort heating, fuels, hydrogen heating, aviation, materials heat treatment, cement, food heating, milk, sterilization, and beverage production under sanitary or sterilized conditions.
Project Costing Principles.
The transition to a greener future has an initial price, which is recovered quickly because of the enhanced efficiencies. The longer the wait by countries and companies, the larger the cost. There are many ways to justify the returns on the capital required for new equipment to replace fossil fuel-burning equipment. Promoting deep decarbonization through Electrification requires understanding the key advantages of Electrification of industrial heating compared to fossil-fuel heating. The returns from rapid investments in large MW electrified equipment can be substantial. This page provides general guidelines for project costing when changing from fossil fuel heating to electric methods. It discusses the costs of various methods, from Electrification to carbon capture. Significant social costs are incurred when using fossil fuels. Read more about the social cost of making CO2.
The most straightforward approach is to use the social cost of GHG production in any cost calculation. This could be $51 to $3000 per ton, depending on the number allowed. Fossil fuel use has a significant social cost and possible taxation. By 2026, the social cost could be $3,700 per ton of CO2 emissions.
Next, the operational savings can be computed by using a modern electric heating system. The benefits could be enormous. First, consider the savings from using electricity for a typical drying system. One can start with the energy benefit. An example we like to tout in the drying sector is that a 6 MW electric system replaced a 40MW fossil fuel system. The operational savings are substantial. 35MW of power in a device for the same objective could save ~US$24.5 million in electric energy costs for the year. This is an easy payback scenario.
Why does electric heating bring in better efficiencies?
Fossil fuel systems are also inherently more complex and inefficient than their electric heating counterparts, with more avenues for failures and loss of efficiencies. The composition of fossil fuels almost always requires heat exchanger Eliminating heat exchangers in hot air heating already saves considerable energy and cost. Burners require an ideal oxygen mixture that must be adequately regulated to operate efficiently, but achieving stoichiometric combustion is unrealistic, such that excess levels of air must be introduced to ensure complete combustion. This excess air is counter-productive by directing heat straight to the flue stack. However, it is a necessary loss since the exhaust temperature must be maintained above dew points to prevent the formation of corrosive mixtures, which can degrade equipment at an accelerated rat Internally, the firetubes can be coated with soot, resulting in a lower thermal efficiency. The upkeep for these systems is extensive because of the complexity of the design — burners, fans, fuel mixtures, exhaust stack temperature, scale build-up, and pollution treatment.
Electric systems are straightforward by design and easily scalable. There are no parasitic losses as there is no combustion, and highly efficient operation can occur without issues. Maintenance includes inspecting a blowdown vessel and electrical connections and ensuring no water or steam leaks. Annual maintenance involves pulling out the element to clean—a process that can be done in an hour. For maintenance and downtime reasons alone, industrial facilities that want to minimize their capital expenditures (CAPEX) and operational expenditures (OPEX) should consider making the switch.
Choosing equipment with high power factor ratings can help reduce reactive power consumption.
Summary:
- The industrial heating and transportation sectors emit almost the same amount of CO2.
- The fastest way to decarbonize is by electrifying industrial heating.
- A 55-KW automobile typically emits one ton of CO2 in 50 hours (or about every 2,500 miles).
- A ~0.8 MW natural gas heater (a typical size in a factory) emits about half a ton of CO2 per hour (the social cost is $51 to $400 per ton of CO2). An industrial heater of this size working for 24 hours could produce 12 tons of CO2 per day. Such fossil fuel heaters also have very low energy efficiencies, thus magnifying the emissions problem.
- One ton of CO2 is made for every half-ton of steel produced.
- The capital costs for electric industrial heaters per kW are lower than those for electric vehicles (EVs). EVs typically have a capital cost of US$5000/kW, compared to US$500- US$1000 for industrial heating equipment.
- When all the costs and improved efficiencies are factored in, large KW to MW electrical heaters can offer much lower overall operational costs than fossil-fuel heaters.
- Industrial electrical heaters are very energy efficient and compact—a 500C 1 MW heater is only 24″ long—and the pressure drops are low—less than 0.1 psig for the 1 MW 800C heater. The low pressure drops benefit space savings, safety from potential explosions, and lower insurance costs.
- Electrification in industrial thermal equipment provides enormous momentum to total global decarbonization.
- Fossil fuel combustion has significant social costs, including direct costs from predated direct taxes on previous emissions [source]. Organizations are now using the social cost of carbon ($51-$3000 or more per ton of CO2 emitted) to assist investment decisions and guide long-term planning by considering the full extent of their operations’ impact on society and the environment. Climate-conscious cities and youth groups are also exerting pressure for change.
- Electrification is the safest and most efficient route for deep decarbonization. About a third of excess CO2 emissions can be attributed equally to industrial heating, transportation, and power generation.
Global temperature rise and CO2 levels are correlated. The global temperature rise promotes intense weather.
Not only are extreme weather events and asset loss events like fires and flooding caused by the rate of rise in temperature, but population extinctions are also related to rising temperatures. The atmospheric CO2 levels 2022 were >410 ppm+, and the temperature rise was almost ~ 1.1 C above a safe preindustrial baseline. In 2024, the temperature is already closer to 1.5C above the baseline, and the atmospheric concentration is close to 421 ppm. Global energy-use-related CO2 emissions grew by ~321 million tons, reaching a new high of more than 36.8 billion tons in 2022. The year 2022 was eventful when the temperatures, extreme climate zeros, and the amount of CO2 in the atmosphere increased. The year 2023 was the hottest on record. If we continue to use fossil fuels, the predictions are for higher CO2 and other GHGs, leading to higher temperatures, higher rates of temperature rise and, consequently, to more extreme weather events.

Rapid steam generation in the industrial heating sector with considerably improved efficiencies (decarbonization) can quickly reduce CO2 and methane emissions to zero. Compare the prices of the lowest-priced fossil fuels in various countries as of 2022 with electric power (source). The project payback is quick.
How can we achieve zero CO2 and NOx with the lowest capital cost? Industrial heaters with high efficiency, high temperature, compactness, and quick on-off features without idling are now readily available. If you have requested a quote for heaters or steam units, please contact MHI for the project cost recovery period. The capital cost per KW for industrial Electrification is estimated to be far lower than that for electric vehicles.
Is there enough electricity available? We think so – even without counting the novel rapid advances in electricity production by sustainable and rechargeable mean Giant batteries that ensure stable power supply by offsetting intermittent renewable supplies are becoming cheap enough to make developers abandon scores of projects for gas-fired generation worldwide. Electric grids have become more efficient all over the world. The efficient use of power may be required as the demand escalates. An efficient use, for example, is using a car battery for other purposes when an EV is not in use – which is almost 90% of the EV’s daily cycle. Efficient use also means using less energy for an objective like Process Heaters, i.e., with a low-pressure drop of only 0.1 psi for 1 MW instead of 1 psi with traditional inefficient electric heaters.
How much CO2 emission is prevented by Electrification? The total CO2 emissions from fossil fuels depend on the fuel and other factors determining the combustion quality (please see the emissions table for specific fuels on the right The Electrification of industrial heating can entirely reduce these rapidly. Typically, using 1 KWh (3,600,000 Joules) of electric energy instead of fossil fuel energy for industrial heating can save at least ~0.18 -0.5 kg of CO2 equivalence from being emitted on average by a heater. Other GHGs like NOx, methane, SO2, or particulates emitted during fossil fuel combustion are even more potent than CO2 and are simultaneously reduced with electric energy use. NOx and methane can be clubbed together into a CO2 equivalence. Any NOx emitted is approximately 298 times more potent than the amount of CO2 (in weight), and methane emissions are 25 times equivalent to CO2 in weight for emission impact.
Updates tropospheric (atmospheric) methane (CH4), (Carbon dioxide) CO2 and (Nitrous Oxides) NOx, concentrations are given here.
Emissions can sometimes occur even before the combustion process when using fossil fuels, e.g., during the transmission or transportation of GHG gases.
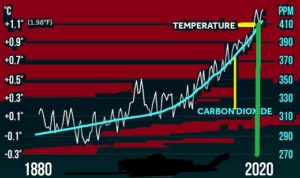
Both CO2 levels and global temperatures are rising, and the generation rate of new entropy is rising.
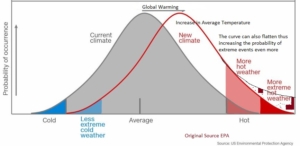
A visualization of how global warming increases the probability of extreme events. Extreme heat-related events increase by shifting and flattening the curve. Earth’s surface warming and rate of warming increase the rate of tropospheric entropy generation demand, leading to unpredictable and severe weather events.
Today, a loss of $283 per ton of CO2 equivalence emission is not unreasonable to add to the project cost (translates to about US$0.15 per kWh of fossil fuel energy). By placing a value on carbon emissions, decision-makers can purchase electrical and industrial heaters with an excellent projected return on capital. Such calculations are shown here. One can expand upon traditional financial decision-making tools with such cost adders and create accurate and proper metrics for measuring investment decisions. As a rough rule, 1 MW of energy production with electricity instead of fossil fuels could save anywhere from 0.2 – 0.7 tons of CO2 emission equivalent per hour. The best option for decarbonization is to quickly change to electrical, industrial heating systems with zero CO2, NOx, and SO2 emissions. Kilowatt-to-megawatt electrical systems are available today with good payback scenarios when considering energy at $0.06 per kWh and only partially including the social cost of emissions.
In addition to the severe cost of CO2 emitted, one should also consider the following factors for a payback analysis:
- The efficiency of thermal transfer. Typically, electrical efficiencies are 30% better than combustion heating efficiencies. On average, MHI Airtorch® systems offer more than 95% efficiency. Process Gas Heaters Comparison Table.
- Pressure drop: Some large MHI models have a pressure drop at 1000C of as low as 0.1 psi (~3wc). High-pressure drops for large flows lead to a higher blower price and PV-energy waste and costs.
- Control system Reasonable control with high-sensitivity instruments offers an excellent turn-down ratio with intelligent cascade electronics, allowing for versatile control. MHI uses the best SCRs and electronics, exceeding typical industry standards.
- Materials and Design. What is the best temperature rating for the Airtorch? Depending on the model, MHI Airtorch® systems offer 1200°C exit temperature. A higher temperature-rated Airtorch® will perform better and last longer even at a lower temperature. See bullet below for productivity as a function of temperature.
- Productivity vs. Temperature (in pdf format Higher temperatures typically lead to faster outputs.
- Improvement of over 30% in energy efficiency compared to …..(click here for case studies)
- Request Information on an Electric Airtorch
The costs of burning fossil fuels are increasing rapidly.
Can one capture CO2 from the air and store it? As of today, direct capture costs are prohibitively high. The range of costs varies between $250 and $600/ton CO2, depending on the chosen technology. Some solids and liquids can absorb CO. Plants naturally remove carbon dioxide from the air. Trees are especially good at removing and storing CO2 from the atmosphere by photosynthesis. Photosynthesis removes carbon dioxide naturally. Amines, algae, zeolites, salt solutions, water, and hydroxides can capture CO. Activated carbon can also absorb CO. The captured carbon dioxide can be used to make value compounds. Still, the CO2 may be given off again. Various reports detail the difficulties and dangers of CO2 capture.
If we add the carbon capture cost to the dangers of CO2 capture and the asset reduction cost of emitting CO2, the actual cost of emitting CO2 could be extremely high for industrial heating with fossil fuels. To limit global warming to less than 2°C above pre-industrial temperatures, current estimates indicate the troposphere must lose or have removed ~1 billion tons of carbon dioxide annually by 2030. Even if the CO2 can be collected from power plants and stored through sequestration, there are two potential problems. The first is cost, and the second is the very high risk of leakage. Carbon sequestration projects can involve storing CO2 in underground reservoirs, which raises the risk of leakage and acidifying water. Some of the craziest unanticipated problems of climate change are: dozens of pristine Alaskan rivers have turned bright orange in recent years because melting permafrost has released high levels of toxic metals into the waterways, a worrying new study reveals. The colorful contamination, which can be seen from space, is a potential ecological nightmare.
Economic: Electric methods are generally more efficient than fossil fuel combustion for heating. Regardless, it is essential to use the most efficient electrical system. Improving energy efficiency can lower utility bills, create healthy jobs, help stabilize electricity price volatility, and improve the climate with lower CO2 emissions for any objective. Several attractive loans are available for curtailing anthropogenic carbon emissions with new equipment, i.e., reducing the emissions of various forms of carbon – the most concerning being carbon dioxide – associated with human activities. These activities include burning fossil fuels, deforestation, land use changes, livestock, fertilization, etc., resulting in a net increase in emissions. The payback period for new equipment for decarbonization is attractively small when one includes the high social cost of CO2 emissions from alternate methods. Contact MHI for your decarbonization system needs (free).
Electrifying industrial heating could be the most rapid method of addressing CO2 emissions in the near term.
Summary of Energy Cost Factoring CO2 emissions: When one includes the social cost of CO2 production, the price of one KWh of electric or combustion energy starts converging. The CO2 emissions per million kilojoules of energy used range from 50.4 kg for natural gas to 68.8 kg for jet fuel. The social cost of emitting industrially produced CO2 is estimated at $51-$3000/ton, rising rapidly with time. Adding climate cost to combustion heating increases the price of all fossil fuels on average by at least ~$283 or more per ton of CO₂ (i.e., corresponding ~US$0.15 per kWh that could be added to the average price of toxic fossil fuel energy costs).
Increased energy efficiency from Electrification can lower greenhouse gas (GHG) emissions and other pollutants and decrease water usage. Converting from a 16MW combustion heater to an electric Airtorch could save over 30% energy and several millions of dollars in climate-reduced asset and insurance costs. A 30% improved efficiency is typically noted in electric heater devices over combustion (fossil-fuel) heaters. For example, a 14.2 MW combustion gas heater could be replaced with an 11 MW electric Airtorc A savings of ~$48,000 daily (assuming 1 KWh ~10 US cents).
Productivity: MHI systems adjust to optimize the energy required by drawing only the necessary power and accelerating productivity at the optimal highest temperature. A higher temperature significantly adds to the production rate. More power equates to a higher energy delivery per unit of time. Conventional furnaces have fixed heat loss; the higher power will mean that you deliver heat faster to reach the required temperature. An underpowered system will struggle to get to the Temperature.
Emissions from Natural Gas. The emissions from natural gas-fired boilers and furnaces could include nitrogen oxides (NOx), carbon monoxide (CO), carbon dioxide (CO2), methane (CH4), nitrous oxide (N2O), volatile organic compounds (VOCs), trace amounts of sulfur dioxide (SO2), and particulate matter (PM).
MHI Airtorch® models are designed for low thermal energy loss. Simultaneously, the the low-pressure-energye-energy loss. MHI Airtorch® models offer high-temperature input, which benefits duct heaters and ovens that quickly replace natural gas heating. This is the best method for decarbonization.
For the best energy saving, the following tips could be helpful depending on the application:
Energy-saving Tips
- If less energy is used for the same objective, it will substantially reduce CO2 emissions. Modern light generators (bulbs) produce the same visible light intensity with much less energy. So does an Airtorch (process air and gas generator) or a modern decarbonized steam generator.
- Improved practice: There is no need to pressurize compressors and bleed them every day, as pressurization leads to substantial energy demand. If using high-volume air flows, ensure the pressure drop is the least.
- Reclaim waste energy. Contact MHI. Regardless, beware of calculations that say preheating air in a fossil fuel heater dramatically improves efficiency. Although about a ~5% gain is possible when otherwise waste energy could be used to preheat the incoming combustion air, if one uses the output useful heat or enthalpy to preheat air, then it does not help. The efficiency should always be calculated as the ratio of useful heat or energy output divided by the total energy input from preheating and chemical bond restructuring. A higher flame temperature equals a higher NOx production. In terms of a global warming climate gas, Nitrous oxides are 298 times more potent than CO2.
- An electric Airtorch device is almost always much more efficient than a fossil-fired heat exchange. Opt for modern electric machines; they generally use less energy for the same objective than a machine with a combustion source. For example, we have shown that an 11MW electric Airtorch® for the same heating objective can replace a 16MW gas heater. Or use an electric instant steam generator instead of a conventional boiler. Or implement methods to conserve the quality of energy.
- Did you know that saving 5MW of power in a device for the same objective (i.e. by improving the energy efficiency) could save over US$3.5 million in electric energy costs for the year?
- There are additional benefits with the MHI Airtorch. The pressure drops for electric Airtorch devices are lower than those of traditional heat exchanger devices. For a 2000 SCFM flow, saving ~5 psi in pressure drop equals about 30 KW in power saving. This is almost a saving of $25,000 per year, assuming a price per kWh of 10 US cents.
- Upgrade equipment. Replace old furnaces and devices with the most modern emissivity heaters, crisp controls, safe insulation, and high productivity. Processes at higher temperatures to achieve the same objective and glean profits from higher productivity. Many thermal process outputs accelerate exponentially with Temperature.
- Productivity vs. Temperature (in pdf format)
- Clean smartly. Cleaning chemicals use a lot of energy, but that energy comes from somewhere. Please keep it clean without adding new chemicals or contaminants. Save energy with high-temperature steam.
- Electric air heating is considered substantially superior to large dies’ flame heating in terms of temperature uniformity. Some examples are discussed below.
High Power Airtorch
Resources |
Click here to view typical applications.
What’s New:: See Testimonials:: Calculate Power:: Conversion Calculator
Airtorch Flow vs. Temperature Charts: Request a quote for Airtorch®
Airtorch® System Introduction
Please use a five-step process for selection. First, choose the maximum rated exit temperature of the Airtorch®. If below 900 °C, please select TA models, e.g., VTA and Mls. If above 925°C, please choose the MVTA or DPF model – please contact MHI.
Sometimes, the lowest power users work through several cycles in a recuperator mode. The SH models can accept inlet gas temperatures up to 800°C. Please get in touch with MHI for details.
The Airtorch® convective system uses a particular class of elements to heat the ambient air and direct that heated air towards a surface or into a chamber. Depending on the model, the Airtorch® system can achieve temperatures ranging from room temperature to 1100-1200°C (~2200°F) with infinitely variable volume flow rates and no harmful emissions, providing a beneficial new heating method with modern controls.
MHI Airtorch® applications are in drying electrical varnish, weld preheating, die heating, plastic softening before forming, drying motor parts, removing moisture, expansion fitting, combustion, simulation preheating and heating molds, curing, prosthetics, heat shrinking, compression molding, flock setting, curing catalysts drying slurries, freeze-drying, improving ink print finish, finishing mirror drying, latex, heating adhesives, and general heating of chambers as shown below. Add to chambers for powder and liquid finishing. Add to continuous furnaces for wood conditioning, metal finishing, and forming. A small but finite temperature drop is experienced when directing Airtorch® flow with insulated piping because of the high velocity.
- For impingement types of applications, the DPFs offer very superior value.
- A good rule of thumb for augmenting uniformity in an existing furnace with an Airtorch® add-on is choosing an Airtorch® power with at least 30% of the original. This may not be enough if a temperature increase is also sought.
- When planning to extend the Airtorch® exit piping, please note that well-insulated pipes will drop the temperature very little as the exit velocity is m/s. A helpful but rough rule of thumb may be about 50°C-100°C/m drop for good internal pipe insulation. Good pipe insulation is specific to whether the pipe is internally or externally insulated. The MHI industry standard is about a 1-2″ thick insulation. Please get in touch with MHI when required.
Introduction to Airtorch® | Airtorch Applications | CalculatPowerower .vs Flow Rate | Easy Design Criterion
With its variable volume flow rate and power adjustability, the Airtorch can be set up to perform at any condition of flow temperature under the curve. Such features offer the user maximum flexibility when applying the Airtorch™ technology to heating applications.
The use of Airtorch® products may be classified into three major categories schematically drawn below. In addition the Airtorch® can be used inline and cross line. MHI is a specialist in inline, offline and cross line Airtorch and other similar systems that heat air and gases to high temperatures.
![]() Direct Impingement | ![]() Gas Preheating | ![]() Retrofit for Enhancement |
Retrofit/Upgrading.
Example of Use to Augment an Existing Furnace Installation for Improved Power and Uniformity.
An example of a 4kW Airtorch® augmentation application is schematically shown below. In this application, many complex-shaped rods are to be heated uniformly. The heat-treater reported that the rods were not uniformly heated in his existing radiant heat furnace. MHI proposed an add-on to his existing furnace with a system of Airtorch products, significantly impacting the uniformity – reducing the total energy consumed. More Green Installation and more Profits to the user. Improve oven performances and eliminate harmful emissions.
A uniform surface heating retrofit example and continuous oven examples are illustrated below.
As a rule of thumb, an Airtorch power of ~0.3 the furnace power is employed when designing for better uniformity.
Electrification is one of the fastest routes to dramatically increase energy efficiency and impact decarbonization. It has the potential to significantly save money and reduce greenhouse gas emissions in the chemical production, test beds, calcination, drying, refining, fuel production, general manufacturing, shipping, and iron and steelmaking industries.
Eliminate GHG emissions: Assuming a cost of emissions of $283 per ton of CO2 emitted, burning fossil fuels for heating could add approximately $0.1 to $0.15 per kWh to the energy cost of fossil fuels.
Another way to consider this is as follows: Replacing a 6 MW fuel-fired unit with an MHI efficient electric heater could result in a 5 tons per hour reduction in CO2 emissions. Therefore, at the lowest emission tax savings (see adjacent column), equivalent to approximately $51 per ton (which could be higher), this results in savings of nearly $190,000 per month. An energy-efficient system also lowers energy costs, depending on the fuel and electricity rates per kWh. If the price is approximately 14 US cents per kWh for both fuels, then assuming a 50% increase in efficiency for an electric 6 MW system, the monthly energy savings could be $300,000. Read More…..
A UN report states that fossil energy sources account for over 75% of global planet-warming pollution and nearly 90% of all carbon dioxide pollution. Several countries have set ambitious goals. The US climate goals (goals set in 2023/2024) are to reduce greenhouse gas emissions to below the 2005 levels by the year 2030 – a step towards a sustainable future (source). The goal requires a 50% reduction in current emissions. The further goal of achieving 100% carbon pollution-free electricity generation by 2035 and a net-zero emissions economy by 2050 underscores the urgency of action. The United States has made significant strides in its climate and energy policies aimed at decarbonization. One hundred ninety-four sovereign states, representing over 98% of the global greenhouse gas-emitting regions, including the US and the EU, have ratified or acceded to the Paris Agreement by 2023. Such global cooperation indicates the shared responsibility in combating climate-changing emissions of CO2 and other greenhouse gases (GHGs). However, the industrial sector must also do its part if the goal of 1.5°C is to be met (the Paris Agreement target).
The International Energy Agency estimates that to achieve carbon neutrality by the middle of the century, global investments in renewable energy must triple by 2030, reaching over $4 trillion annually (cited from a wiki source).
Because of the health and climate problems associated with GHG emissions one has to ensure that GDP and firm level growth can increase even as fossil fuel use comes down, primarily through improvements in energy efficiency and going electric. The International Court for Justice ruled in July 2025 that countries can sue other countries for climate emissions. It is a non-binding ruling but the directions that countries must adopt to prevent carbon emissions is clear.
Solution
Choose from electric Airtorch, Steam, or Radiative panel products to eliminate GHG production. Often, electricity (electric energy) is almost free.
Case Study: Aluminum melting requires 397 kJ/kg of energy, but many fossil fuel direct furnaces are only about 13% efficient. Energy efficiency could be improved five times by using electric methods, e.g., Airtorch.
Case Study: A reduced coking tendency and higher conversion temperatures can be expected while converting Naphta (cracking) or similar compounds to simpler olefins or more valuable smaller molecular fuel. Contact.
Power conversion MW to Btu/hr (Multiply by 3412142)
0.01 MW | 34121.42 BTU/h |
0.1 MW | 341214.2 BTU/h |
1 MW | 3412142 BTU/h |
2 MW | 6824283 BTU/h |
3 MW | 10236420 BTU/h |
4 MW | 13648570 BTU/h |
5 MW | 17060710 BTU/h |
6 MW | 20472850 BTU/h |
7 MW | 23884990 BTU/h |
8 MW | 27297130 BTU/h |
9 MW | 30709270 BTU/h |
10 MW | 34121420 BTU/h |
Ask MHI about compact KW to MW electrical systems. MHI products for heating and steam do not use any fossil fuel nor emit greenhouse gases. Using fossil energy like fuel oil, gasoline, or natural gas for heating creates considerable CO2 and other greenhouse gases. Every ton of CO2 emission causes about the same amount of global warming, no matter when and where the CO2 is emitted. (Free calculator).
Why is there so much efficiency gain with electrification compared to fossil-fuel heaters?
This is mainly related to inherent thermal energy loss from flames (short wavelengths) and the natural inefficiency of heat exchangers. Conventional drying is an open process where flame radiation causes heavy energy losses. When drying is done by directly heating the bed with combustion burners, the flue gases take away a lot of energy. There is a 20% to 50% loss when heat exchangers are employed. Without a heat exchanger, the energy efficiency is always better. Ask MHI about Waste Heat Recovery (WHR) Systems.
Specific fossil fuel emissions of CO2 per GJ of heating specific fuels.
The heat value of fuels (MJ/kg of fuel) | |
Natural Gas (the main component is methane). Heat value 42-55 MJ/kg. | 50.4 – 56 kg of CO2 per GJ |
Jet Fuel Heat value 50-55 MJ/kg. | ~68.8 kg of CO2 per GJ |
Bituminous (coal) Heat Value ~ 18 MJ/kg. | 88.8-100 kg of CO2 per GJ |
Diesel and Home Heating Fuel (Distillate Fuel Oil) Heat Value 42-46 MJ/kg. | 59.9-69.3 kg of CO2 per GJ |
Gasoline and Ethanol Blends. Heat value 44-46 MJ/kg. | 64.1 -72. 5 kg of CO2 per GJ |
- The tropospheric entropy generation rate (EGR) is already high and increases with temperature.
- On average, one ton of CO2 requires fossil fuel to burn approximately 4 million kJ.
- About two ppm of CO2 is added to the troposphere annually by fossil fuel combustion. This significantly raises the production demand of the tropospheric entropy density rate by almost ~ 10−8 J/(m3.K.s.ppm(CO2)). Citation.
- One industrial process heater using fossil fuels (15MW) could use 245 Billion BTUs for a year. That corresponds to a lot of CO2 production—about ~100,000 tons or more of CO2 emissions from one such large industrial dryer yearly!
- The social (environmental) cost of producing/emitting CO2 gas varies—several hundred dollars per ton of CO2 emitted—and is climbing rapidly (Source).
- Climate change impact impacts the cost of a project. Companies today include the environmental cost in project economics calculations.
- Thus, the social cost of using a carbon-containing combustible gas could substantially increase the price of combustion fossil fuel projects.
- Did you know that Modern Electric Heating methods Eliminate CO2 Emissions?
- How much CO2 can I save by going electric? A 10 MW decarbonized machine can prevent several Tons of CO2 emissions every hour. See more…(pdf format)
- So why not go electric? Electric heating is more efficient for energy use in addition to zero GHG emissions benefit. An excellent place to start is industrial decarbonization. Save energy with efficient electric systems.
The Gamut of Airtorch Products
A fuel’s “Heat value” is the heat released during combustion. Also referred to as energy or calorific value, the heat value measures a fuel’s energy density and is expressed in energy (Megajoules or Gigajoules) per (kg). If the fuel contains carbon, there is CO2 emission, as shown in the table above.
Fuel | Heat value |
Hydrogen (H2) | 120-142 MJ/kg |
Methane (CH4) | 50-55 MJ/kg |
Methanol (CH3OH) | 22.7 MJ/kg |
Propane (C3H8) | 46 MJ/kg |
Dimethyl ether – DME (CH3OCH3) | 29 MJ/kg |
Petrol/gasoline | 44-46 MJ/kg |
Diesel fuel | 42-46 MJ/kg |
Crude oil | 42-47 MJ/kg |
Liquefied petroleum gas (LPG) | 46-51 MJ/kg |
Natural gas | 42-55 MJ/kg |
Hard black coal (IEA definition) | >~23.9 MJ/kg |
Hard black coal (Canada) | ~ 25 MJ/kg |
Sub-bituminous coal (IEA definition) | 17.4-23.9 MJ/kg |
Sub-bituminous coal (Canada) | ~ 18 MJ/kg |
Lignite/brown coal (IEA definition) | <17.4 MJ/kg |
Lignite/brown coal (Australia) | c. 10 MJ/kg |
Firewood (dry) | 16 MJ/kg |
Natural Uranium in LWR with U & Pu recycle | 650 GJ/kg |
Natural Uranium, in FNR | 28,000 GJ/kg |
Uranium enriched to 3.5% in LWR | 3900 GJ/kg |
Steam OAB Unit 360 view Video (download).
A uniform surface heating retrofit example and continuous oven examples are illustrated below.
As a rule of thumb, an Airtorch power of ~0.3 the furnace power is employed when designing for better uniformity.
EFFICIENCY
Electric Systems Offer Design Improvements / Enhancements | ||
Combustion/Flame | MHI Electric Systems | |
Appearance | Non-uniform heating. | Repeatable uniform heating – resulting in consistent label results. Once conditions are dialed in, the setup will yield minimal variation. |
Bottle or Treated Surface | Combustion leaves deposits on the surfaces (visible to micro level) | Airtorch® or Steam or Steam/ Air patented heating leaves no combustion product on treated surfaces. Improves detail and appeal. |
Sources | Combustion source creates: Explosion hazard Costly fuel and disposal Emissions of CO2 from combustion ‘Hot’ spots from flame heating Venting required | Electric Systems: Electric flexible source. Air or Water No emissions No combustion Evenly distributed heat No explosive consumables |
SUSTAINABILITY
Modules for a Green Work Environment | ||
Combustion/Flame | MHI Electric Systems | |
Modularity | New gas lines, more consumables used, safety approvals, etc. | Modular with flexible power lines as needed. You can add and subtract modules in minutes. Easy to install Easy to operate Easy change of configuration Highly mobile |
Repeatability | Non-uniformities result from combustion treatment surfaces— uneven heating, combustion deposits, NOx, SO2, and more. | Electric systems offer uniform, repeatable, and continuous treatment of products resulting in less variance. |
Control | Lack of precise control from combustion is a problem. | Precise control of temperature and output gives high efficiency to your process. A high level of control also allows for protection features such as overtemperature protection. |