Airtorch® Applications
Climate change is one of the most significant challenges of our time. As the world looks to curb climate change, switching to efficient electric methods with a zero-emissions transition could spur huge economic gains. The compact Airtorch® can eliminate fossil-fuel heating, rapidly aid deep decarbonization, and create flexible energy-efficient processes.
The Airtorch® is a state-of-the-art electric process gas heater that replaces traditional fossil-fuel heating methods. It provides numerous advantages regarding efficiency, versatility, and environmental impact. It can be used from 100C to 1200C to save energy, operational costs, and climate-impacting GHG emissions.
Airtorch® Technology Overview: Key Features of an Airtorch®.
- High Energy Efficiency:
- Electric Heating: Nearly 98% efficient, eliminating CO2, NOx, and SO2 emissions associated with fossil-fuel combustion.
- Controlled Heating: Offers precise temperature control, improving process efficiency.
- Robust Construction:
- Long-lasting: Built for durability and extended operational life.
- Compact Design: Space-saving and easy to integrate into existing systems.
- High Temperature and Pressure: Capable of operating at high temperatures and pressures. High Pressure. Large MW.
- Versatile Applications:
- Kilns for calcination, ceramic tile manufacturing, glassmaking, mineral spray dryers, aluminum melting furnaces, ceramic kiln heating, and drying.
- Set the optimal gradients for thermal or power optimization.
- High-Pressure Test Stands: Used in automotive and jet engine testing setups, including wind tunnels.
- Fuel, Nano-Structuring and Chemical Reactions: Suitable for gas mixtures like hydrogen, methane, or syn-gas, enabling combined catalysis.
- Materials Processing: Applied in cement, food and beverage production, drying, heating, stucco, calcining, sintering, melting, catalysis, fuels, and other chemical reactions.
- Food Industry: For various food preparations such as juicing, liquids, dried fruits, peanuts, and walnuts.
- Petrochemical Operations: To heat hydrocarbon feedstocks to temperatures between 700–1,000 °C, where heaters separate natural gas from water, oil, or other chemicals. Replaces traditional heaters.
- Additional applications up to 1800 °C in materials processing (beyond Airtorch click).
- Large comfort applications.
- Climate abatement solutions.
- Industrial drying
Economic and Environmental Impact of Patented Airtorch Models.
- Cost-Effectiveness: Rapid paper drying at 450°C using the Electric Airtorch can result in significant energy savings compared to gas burners, which are typically 50% efficient.
- The Aluminum Industry generates around 1.1 billion tons of CO2 annually. Airtorch units can produce the required temperatures instantly, cutting down on energy usage and eliminating CO2 and other GHG emissions. use to 1200°C
- Food Drying: Efficient drying methods can save energy and reduce transportation costs.
- Petrochemical operations to heat hydrocarbon feedstocks to temperatures ranging from 700–1,000 °C. Fractional distillation: Heaters are used to separate crude oil into its components based on boiling point for thermal cracking, where traditional heaters break down. hydrocarbons into products like ethylene—gas processing- where heaters separate natural gas from water and oil.
- Offshore operations: Heaters prevent hydrates from forming in subsea pipelines or recapturing waste heat from steam or CO2.
- Advantages of Electric Heaters
- Efficiency: Electric heaters like the Airtorch are highly efficient, converting almost all energy into heat. Extremely low piping requirements.
- Lower Operating Costs: Despite higher capital costs, electric heaters have lower operating costs due to their efficiency and lack of need for gas plumbing or combustion insurance.
- Environmental Benefits: Electric systems can prevent significant CO2 emissions, reducing the social cost of fossil fuel combustion.
- Velocity and reaction control during distillation processes.
- Control over heat up rates.
- An example case study for heating simulation or heater stages highlights a company that achieved significant energy savings by converting from combustion to electric heating using the Airtorch®. The social cost of producing even one ton of CO2 and methane can be very high. The US Interagency Working Group on the Social Cost of Greenhouse Gases estimates the social cost of methane emissions at US $1,756 per short ton.
Industrial Products and Fuels for a Decarbonized Economy: Several industrial sectors, such as manufacturing, energy, cement, drying, food, and chemicals, seek tested sustainable alternatives to conventional fossil fuel and low-energy-efficiency heating equipment. According to recent 2023 US government reports, achieving meaningful reductions could require up to $1,100 billion in capital expenditure and a bold shift in leadership and technology adoption across various sectors. Carbon-intensive industrial sectors are facing a critical inflection point while society is focused on accelerating deep decarbonization,
An example of why decarbonization is cost-effective: For rapid paper drying at 450C, 1000 KW and 6600 Nm3/h of dry air can be used (approximately). More air means faster and uniform drying. Hot air has no moisture, so drying is very fast. In contrast, combustion air has a lot of moisture, so one could waste much energy with combustion or lose efficiency in heavy, non-efficient heat exchangers. One of the advantages of using the Electric Airtroch is that the energy savings are significant. Gas burners lose a lot of radiative heat and drag in moisture. Gas burners are typically 50% efficient for heat (it should be noted that some gas burners even claim 85% efficiency), whereas electric ones like the Airtorch are nearly 95-98% efficient. The energy savings from using electric heaters are usually significant. There could be slight differences based on the gas burner. Other advantages are that the whole operation can be below the paper ignition temperature, whereas gas burner drying is with flames. A reduction of 41 MW to 4 MW by converting to electric has been seen in Europe.
Many aluminum fossil fuel melters are only 13% efficient, whereas electric meters are likely to be much more efficient. The aluminum industry generates around 1.1 billion tons of carbon dioxide pollution annually. MHI’s Airtorch units can produce the required temperatures instantly and, because of their efficiency at all temperatures, can reduce energy usage while eliminating CO2 and other GHG emissions.
Drying or dehydrating food is a method of preservation that removes moisture, which prevents bacteria, yeast, and mold from growing and spoiling the food. Drying also slows down enzymes, which are natural substances that cause food to ripen. Drying raw ore makes transportation much more economical by removing the bulk of the moisture from the material, so producers are not paying to transport water weight and can utilize fewer transportation units. Drying is accomplished by several techniques, like passing the web around a series of steam-heated cylinders on a paper machine. Drying is almost always aided by vibrating, shaking, tumbling, and any other method that exposes wet surfaces and prevents moisture gradients. One should also consider water as a fiber wall component since fibers are completely soaked when the sheet of paper is formed. After drying, nearly all the fibers in the paper collapsed, taking on a strong ribbon-like structure. Electric dryers and calciners substantially reduce energy use and costs with no GHG emissions. Drying is a high-energy process in a way that almost 20–30 % of the energy consumption in industrial heating is for drying – more than 447.1 quadrillion Btu.
The capital cost of electric heaters is higher than that of combustion equipment. Still, one may see quick savings because of the efficiency of heat conversion and a lack of need for gas plumbing or combustion insurance requirements. Contact MHI for payback calculations. For continuous-use operations, the energy cost is less (because of the efficiency), so there is a rapid payback if that is the case. Also, furnace erosion is low. Anyway, the social cost is very high today for emitting CO2. A 1000 KW electric system can prevent about 300-600 kg/hr of CO2 emission. Each kg of emission has a social cost of almost $51 – $500 or more/kg. It is different for every country and government. Regardless, it could be a significant savings, almost $1500 per hour for a 1000KW Airtorch compared to the fossil fuel combustion type of flame heaters.
MHI offers a range of powers – all with high energy efficiency. Airtorch models – KW to high MW range are efficient and compact, designed to aid in significant decarbonization with improved energy efficiency. The Electric Airtorch® is a unique low-pressure-drop patented device used to heat air and other process gases quickly to a temperature ranging from 20°C to 1300°C. Drying, test stands, Pneumatic conveying, Chemical processes, Exhausting, Thermal oxidation, Combustion air, Aeration, Calcining, Air knives, Sealing, packaging, antimicrobial applications, heat treating, cement, stucco, food and beverage, paper and pulp, ore drying, metal extraction ad processing are some of the typical applications.
Use the Airtorch for electrifying high-temperature industrial processes in aluminum melting, iron-making, magnesium production, glass furnace decarbonization, alumina calcination, solar cells, ore drying with controlled humidity, cement, bauxite roasting, and other feedstocks, and lime production. Large Airtorch® uses from KW to MW are seen in Jet Engine Test Beds, Paper drying, Molasses drying, Automotive Engine Test Beds, Chemical Synthesis, Digestion, Clay calcination, Cement Industry, Drying, or Direct Reduction Processes. They find use in simulating heating in replacing combustion burners and preheaters, test rigs, cementitious process running power plants, large die heat-up, chemical and metallurgical processes, fuel production, and replacing fossil fuel calcination & kiln firing in several industries, including cement-making, system combustion/flow simulation, additions to cement clinker furnaces, curing, drying, or bonding of paper boards, removal of inorganic and organic salts, fuel cells, thermal energy storage, general heat treatment for bending and de-flashing/deburring, drum heating, plastic rolls, welding of plastics, soldering disinfection, drying, rapid paper, and pulp production, burner burn off, Electric heater for wind tunnels, chemical reactions for environment and sustainability applications, and general uniform heat g requirements. With devices like the Airtorch and similar high-value equipment, there is the potential to decarbonize roughly 80% of US petroleum refining subsector CO2 emissions by 2050.
What is a decarbonized economy? A decarbonized modern economy has low greenhouse gas emissions from its industrial, transportation, and power generation sectors. The impact of decarbonization can be rapidly achieved by converting fossil-fuel combustion methods to electrical methods. It is straightforward to convert combustion heating and drying to electrical heating and drying. For 1 kWh of energy use or energy conversion by electric methods instead of burning carbon-containing fossil fuels, about 0.8 – 3 lbs. of CO2 production can be prevented. A 100 KW device can prevent 80 – 300 lbs. of CO2 from being made every hour when electrical heating is employed instead of combustion or fossil fuel heating. There are no anticipated drawbacks to decarbonization by electrification because the sizes of electric units available today are very compact. Process heating represents the most significant energy use and the largest source of GHG emissions in manufacturing. In 2018, process heating accounted for 31% of sectoral energy use (7.5% of economy-wide energy use) and 51% of sectoral energy-related GHG emissions (10% of economy-wide energy-related GHG emissions). Direct energy use for process heating in the manufacturing sector includes fuel combustion (66%), steam (30%), and electricity (4%) (source DOE Roadmap). When the fuel used to generate steam and electricity is considered, at least 95% of the energy used for process heat is derived from combustion, including fossil fuels and waste/product fuels. Furthermore, about one-third of energy consumed in providing process heat is ultimately lost as waste heat. Compact MW units are available for heating, efficient chemical, and fiber drying processes directly or as thermal storage batteries.
Case Study: A 14.2 MW gas-combustion process air heater to a 12 MW MHI Electric Airtorch is a $3 million per year saving assuming 12 months, 30 days a month, and 24-hour days. The social cost of the CO2 emitted by burning natural gas has not been factored into this calculation. Review energy calculations. With over 5 billion metric tons of CO2 emissions in the United States in 2017, the utilization and conversion of CO2 into value-added chemicals, fuels, polymers, building materials, and other carbon-based products represent an economic opportunity. The MHI Airtorch and MHI steam generator products can be considered for such use.
Case Study: A 13 MW unit for calcination- with 200C inlet and 750C outlet or for cookers – 350°C, inlet and 1200C outlet temperature, with variable moisture loads g/kg or for Drying 200C inlet and 350C outlet with 800g/kg moisture load or for ventilation.
MHI Airtorch has a low-pressure drop of 3 millibars or higher.
Case Study: Several industries make steam in processes like calcination, digestion, alkali reaction processes, etc.; currently, fossil fuels are used for the heating required in such processes. Such processes can quickly be decarbonized with the Compact Electric Airtorch (a typical 1 MW, 480V Airtorch is only 24″ in size) or dried with a steam-airtorch. The steam or other effluents generated from such processes can be further heated or reheated and returned for use at a high temperature with Airtorch® systems. Such chemical returns can be used for electricity generation, chemical production, hydrogen production, and other forms of “work” in steam turbines, melting, or sustaining chemical reactions, yielding a very high Carnot efficiency increases with Th (the hot temperature). The Carnot efficiency is (Th-Tl)/Th, where Tl is the condensation temperature. Thermal batteries are available from MHI.
Case Study: Melt aluminum in a decarbonized way with the Airtorch. Add a bit of nitrogen to the electrically heated air to reduce dross. Melting 7000 kg/hr of aluminum requires only a compact 780KW Airtorch. Indirect fossil-fired furnaces are as low as ~13% efficient, whereas electric furnaces for melting aluminum could be 60-90% efficient.
- A 1MW electric system will prevent 0.25-0.6 tons of CO2 emissions per hour from being emitted. Source: https://www.epa.gov/energy/greenhouse-gas-equivalencies-calculator-calculations-and-references
- Replacing a 5 MW burner with a 1.2 MW Electric Airtorch® could save 76% energy. Even if the electric energy is 1.5 times the price of equivalent fossil energy price, there is approximately a savings of 3 times in energy costs per year with the conversion (5MW current gas furnace being replaced by 1.2 MW electric). Free calculators listed here.
- Electric energy users will also experience a benefit revenue if climate costs are a factor (like a climate tax for CO2 emissions) for payback/ revenue calculations. In the US, anywhere from $51 – $4000 could be perhaps allowed in project costing). Here is a source https://en.wikipedia.org/wiki/Social_cost_of_carbon.
- For the Airtorch functionality, there is no difference between Air and N2 use. As you already know, using N2 gas or adding N2 gas to the air supply should reduce dross.
Case Study: The drying time of industrial dryers is influenced by various factors, including moisture content, material type, heat transfer method, dryer design, and airflow. Manufacturers can reduce drying time and improve overall productivity with the Versatile Airtorch. With further advancements in decarbonized dryer technology and process optimization, the industrial drying industry continues to evolve, providing faster and more energy-efficient solutions for various drying applications.
In conclusion, using an electrical Airtorch has many benefits because of its efficiency and control. Efficiency as high as 98% enables a strong return on investment and quick payback periods.
Decarbonization with Energy and Cost Savings with an MHI process gas heater
See below for many other uses of the Airtorch, such as wind tunnel heaters. Choose from compact 40KW to 200 MW systems 690V, 600V, 480V, 400V, and other standard country-specific three-phase voltages.
Thermal processing companies worldwide are pressured to lower their operations’ environmental impact and make them more sustainable. These pressures come from governmental regulations and societal expectations, resulting in increasingly stringent requirements. Many companies are accelerating their “green” initiatives and programs to leap ahead of these regulations and lead such transformation for their industry. MHI Airtorch® and MightySteam® can assist your various initiatives. Decarbonize the industrial sector, the agricultural industry, and the building sectors. Cut emissions and decarbonize with MHI products. Use in thermal oxidizers and catalytic oxidizers: Thermal oxidizers are typically used in giant factories that produce higher exhaust volumes.
In contrast, catalytic oxidizers are more commonly used in smaller facilities or where the VOC concentration is higher. Both can use Airtorch heated air at a fraction of the cost of polluting fossil fuel burners. For energy benefits in any application, from comfort heating to heavy industrial processes, the Airtorch® is an excellent approach to tackling climate change.
Why Use Electric Process Gas or Steam Heaters?
- The energy cost produced by electric or combustion methods is not that different when the social cost of harmful CO2 is considered.
- Electric heating gives precise temperature control with fast response times.
- Very low-pressure drops save considerable energy.
- Electric heating is ideal for uniformly heating gases and other fluids to high temperatures.
- Electrically heated Ai torch® systems make unlimited turndown feasible with precision.
- For example, MHI Airtorch® units of 240 KW or 45 MW offer a 90 % turndown when required.
- Suitable for use in hazardous areas, including external use.
- There are no in-plant emissions. The most important crisis facing us is the ecological crisis caused by emissions. Emission control is addressed using the best efficiency (system and rules) and new technologies that can benefit from high-efficiency electrical energy.
- Contact MHI.
Home Page: Process Air and Process Gas Airtorch® Models.
WHY CHOOSE THE BEST AVAILABLE ENERGY-EFFICIENT AND DURABLE PROCESS HEATER? Did you know devices used at ~1000°C could last exponentially longer at 700°C? MHI can often provide a full warranty for an Airtoch® that covers the heater. Check testimonials from customers. The outlet temperature is 20°C-1200°C. Choice of shell pressure. New high-value, highly compact duct modules are now used to transform combustion ovens into electrically powered heating ovens. Ask MHI for the best warranty on heating systems. Why is decarbonization a competitive advantage? Contact MH about changing from fossil fuel combustion to preheating.
Home Page: Process Air and Process Gas Airtorch® Models for Catalytic Packed Bed Heating.
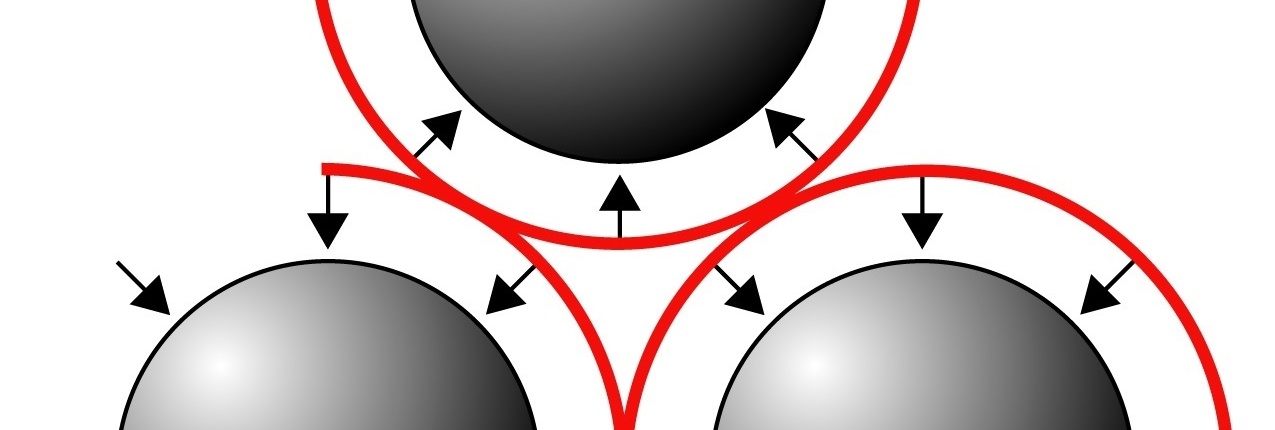
Uniformity with Airtorch® In almost all cases except for very tiny beds, it is generally considered better to use hot gas to heat a catalytic bed rather than resistance heaters, primarily because hot gas provides more even heat distribution throughout the catalyst bed, leading to better efficiency and known reaction rates in the catalytic process. Such gas heating helps with better heat transfer, flexibility in temperature control, and better temperature distribution. It is perhaps the only scalable way to prevent hot spots. This is a low-maintenance cost approach. Such a method also provides flexibility with heat recapture and variations in catalyst use if required.
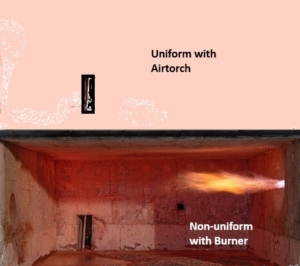
Uniformity in a fossil fuel heated furnace with expected uniformity in an electric hot gas heating method
Process Air and Process Gas Airtorch® Models (120/240/400/480/600V). MHI Airtorch® models are extremely energy efficient.
They are manufactured to ASME specification-compliant and built by an experienced company with patented technology for uniform, trouble-free heating. Airtorch models range from 1 KW to several MW. The smaller KW models are LTA, VTA MTA925, while GTA925—the larger flow models are MVTA and GTA (high-pressure) classes. MHI staff and technicians are committed to excellence.
To help with bacterial or virus losses, use the steam products and Airtorch® Products for rapid field sterility.
Let us help with Industrial Decarbonization.
DEEP- DECARBONIZE
Decarbonizing the industrial sector is very important to address our climate crisis. Almost a third of the greenhouse gas emissions are from the industrial sector. CO2 emissions can be reduced quickly, as can emissions from the fuel-making, general industrial heating, and chemical and steam sectors. The first steps in decarbonization are eliminating heat production by fossil-fuel-fired combustion and relying on electrical energy instead of heating. This can significantly impact CO2 emissions; e.g., the cement industry produces about 10% of global human-made CO2 emissions, of which about 60% is from the chemical process and 40% is from burning fuel.
Although switching to high-quality clean energy may initially appear costly, the benefits are astounding. Between 1990 and 2018, greenhouse emissions from America, Europe, and other regions decreased by ~23%, while the economy grew by 61% (click for reference). Not bad. However, the atmospheric (tropospheric) CO2 content continues to rise, causing a positive rate of Earth warming. This triggers erratic weather and causes asset losses. Per kg of CO2 emitted, the social cost is extremely high for fossil fuels’ full use. However, much more can be done using the Electric Airtorch or the MightySteam(R) steam systems.
Methane emissions are of great concern for global warming and climate change. Did you know that Methane has a global warming potential of almost 25 compared to carbon dioxide? The uses of the Airtorch include cracking cold gas (the cracking process), i.e., for naphta or ethanol for ethylene or carbon black production. If one is considering bio-fuels or valuable products like carbon monoxide (CO), formic acid (HCOOH), Methane (CH4), ethylene (C2H4), or ethane (C2H6) from CO2 conversion – please get in touch with MHI with your requirements. Heat without chemical or energy wastage, e.g., methane or other petrochemical gases, can be heated to have the least residence time and prevent coke formation.
What is Green Steel? Steel that does not contain carbon. Iron ore is reduced at about 850C with hydrogen to make such steels. The carbonaceous (coke) reduction methods commonly used to produce iron are not employed when making green Steel. Consequently, there is no carbon present in iron or steel. Hydrogen-based direct reduction uses hydrogen instead of coal as a reagent to reduce iron ore to pig iron, eliminating the CO2 emissions from the equivalent process in a traditional blast furnace.
Drying. Cement, Gypsum, Paper, Ores, Silicates, Carbonates., Calcining
The microstructure of steel is conditioned such that it competes with carbon steel, which has valuable properties of strength, flexibility, and toughness. Green steel production also avoids secondary carbon-reducing processes like the Basic Oxygen Process. Green steels could include alloying elements like hydrogen, oxygen (see above for Fe/FeO composites), nitrogen or boron, aluminum, manganese, vanadium, molybdenum, etc. The chart below shows the power of critical carbon-containing steels and some without carbon.
Electric heating improves energy efficiency. Electric heating prevents CO2, NOx, and SO2 emissions associated with fossil-fuel combustion heating. Some recent estimates suggest that global carbon dioxide emissions from fossil fuels will hit a record high of 36.6 billion tonnes in a few years, corresponding to a record high of 442 ppm in the atmosphere.
Syngas (synthesis gas) is a mixture of hydrogen and carbon monoxide in various ratios where electrically heated hydrogen or plasma-dissociated CO2 or steam is employed, depending on the type of reaction. Electrically heated hydrogen, or sometimes high-temperature carbon monoxide, is often used as an ore reduction fuel [95,97]. Such gases may contain some carbon dioxide and methane. Alcohol and its derivatives are regularly produced with a two-step industrial process for catalytic hydrogenation of syngas into methanol (CO/CO2 + 3H2 → CH3OH + H2O). Subsequent catalytic dehydration of the methanol over catalysts can produce DME (2CH3OH → CH3OCH3 + H2O), which is often considered an alternative to diesel fuel. Multi-functional catalysts can be used in scalable electrically heated reactors. An illustration is shown below.
Energy Savings and Project Costs with the Electric Airtorch. Click here.
Case Study: An example of one company saving significant energy costs by converting from combustion to electricity. Did you know that the social cost of producing even one ton of CO2 and Methane can be very high? The social cost of methane emissions into the atmosphere is estimated at ~ U.S. $1,756 per short ton by the U.S. Interagency Working Group on the Social Cost of Greenhouse Gases.
The social cost of C02 is about $283/ton. Other fossil fuel combustion emission gases, like NOx, including NO2 and N2O, and other nitrous oxides, have much higher CO2eq.
Electric heating is controlled and offers process benefits in even the most challenging applications.
Heating parts and drying with efficient electrically heated air with zero CO2, SO2, particulate, or NOx emissions offers improved uniformity and energy savings compared to flame heating.
Typical Applications for Airtorch®:
- Several applications are in high-pressure test stands for automotive and jet engines. Key Features include long-lasting, high temperature, high energy conversion, high pressure, and Compactness.
- Electric hot air generators are often used to heat commercial and industrial environments. Several applications are in energy-efficient comfort heating. Key Features include Compactness, long life, and rapid heating.
- Several applications in chemical processes and drying. Key Features: Energy efficient, extremely compact, controlled high temperature, and rapid heating. MHI Airtorch® nano-structuring is used for various gas combinations like hydrogen, methane, or syn-gas. Combined catalysis action is enabled.
- Use in Ammonia, Cement, Steel, Aluminum, Calcination, digestion, Drying, and general heating or preheating industries.
- Use Steam Airtorch for heating steam gas.
Each type of application has its unique control system and long-life materials designed for that market.
Case Study:
Kilograms of CO2 emissions per million KJ (kilojoules) (Source) | |
Natural Gas (the main component is methane) | 50.4 |
Jet Fuel | 68.8 |
Bituminous (coal) | 88.8 |
Diesel and Home Heating Fuel (Distillate Fuel Oil) | 59.9 |
Gasoline and Ethanol Blends | 64.1 |
A customer replaces his 16.5 MW natural-gas hot-air generator with an 11.5 MW electric hot-air generator (Airtorch®). Both units convert 28000 SCFM from room temperature to 700°C. What are his energy-saving and CO2 production savings? Answer: Considering 17 psi savings in pressure drop, a unit efficiency from the improved new technology, and the elimination of the combustion process, the user could save ~40% energy. Please contact MHI. for details.
Summary: The MHI Airtorch® can save up to 52800KWhr of energy daily and prevent producing 57954 Kg per day of CO2 (assuming an 8-hour day). For details, Contact MHI.
CO2, SO2, and NOx (including N2O) prevention with energy savings. Did you know that each such unit can cause savings estimated at $44 Million over a ten-year lifetime? Please contact MHI. for details.
Sectors for Decarbonization
Almost ninety percent of the industry’s GHG (Green House Gases) emissions are Methane and CO2. Almost 40% of the industry’s CO2 emissions today (2018) result from manufacturing the four industrial commodities—ammonia, cement, drying, calling, sintering, ethylene, and steel. A significant amount also comes from the general heat-treating industry.
Decarbonize chemicals and fuel making. Contact MHI.
Preheat to reduce fuel/ carbon for oxidation. Contact MHI.
Decarbonize kilns and ovens for brick making and tiles. Contact MHI.
Decarbonize Iron and Steel (see below). Use for primary and secondary aluminum production. Heat H2 gas economically. Contact MHI.
Decarbonize food and beverage Products. Contact MHI.
Decarbonize all Furnace Preheating. Contact MHI.
Decarbonize/Calcine Alumina (Bauxite), Cement, Clay, Lithium, and Other Ores. Lime and Concrete (see below). Contact MHI.
Decarbonize Paper and Forest Products (see compact energy-efficient drying technologies below). Contact MHI.
GTA. MegaWatt Airtorch has robust holding ears for easy mounting.
Catalyst and reactor beds.
Electric heating of catalyst beds and Fluidized beds is uniform for large-scale heater beds
CHEMICAL REACTIONS
Low-carbon energy inventions and innovations are essential to combat climate change, promote economic competitiveness, and achieve strong energy security. MHI’s rapid heat and high-temperature gas and steam systems have been tested for several uses, such as eliminating combustion heating and enabling new chemical reactions. Closing the carbon cycle using excess CO2 is an appropriate intermediate step toward a carbon-free future. The use of the powerful Airtorch® for continuous VOC removal, conversions, ore drying, rapid heat treatment, and surface treatments like finishing to hardfacing is the future. The C, CO, and CO2 gas reactions, including the Boudouard, Fischer-Tropsch, DMR, and variations, can be manipulated with hot process gases – including Air, N2, O2, CO2, Ar, and more. Examine other reactions below and do not hesitate to contact MHI for guidance:
2CH4 + H2O +CO2 = 3CO + 5H2 Well feasible above ~(760-860C) with easy methods for enabling all forms of downstream reduction. MHI reaction.
E.g., products that are reducing gases that can be used for various reducing reactions, including cleaning and shiny metal production, such as Fe2O3 + 3CO = 2Fe + 3CO2 (weak) or Fe2O3 + 3H2 = 2Fe + 3H2O above 520C. Note that CO2 + CH4 =2C + 2H2O is always feasible at >100C but is extremely weak. Fe2O3 + 2CO + H2 = 2Fe + 2CO2 + H2O is always feasible but best above 1100C. The reaction Fe2O3 + 3H2(g) = 3H2O(g) + 2Fe is feasible above 600°C but requires a higher temperature than that for proper kinetics. Fe3O4 + 4H2(g) = 4H2O(g) + 3Fe is feasible above 1100°C. FeO + H2(g) = H2O(g) + Fe is a difficult reaction. Some green steel processing could use a mixture of Fe2O3 and nano-FeO, which, when reduced, can yield a metal-ceramic composite of Fe/FeO.
Or say:
CO2 + CH4 = 2CO + 2H2. Feasible above ~660C or via the steam reforming and water shift shown here.
Unique combinations may be used for advantageous reaction engineering.
2H2 + CO2 = C + 2H2O is feasible below 600C
H2 + CO2 = CO + H2O is feasible above 900C
MHI offers 1-20 Mega-Watts, easy on-off reactors, with Airtorch® models. Contact MHI.
Is sustainable CO2 reuse via the Dry Methane Reforming (DMR) process cost-competitive?
Pyrolysis of Methane at high temperatures can produce hydrogen and other carbon-hydrogen compounds or various morphologies of carbon like C12, carbon -fibers, and other useful high-energy products and materials. Several reactions are possible that can be manipulated with pressure and catalysts:
CH4=2H2+ C (At 1000C K= 1 x 10^2, Delta(H)= positive)
2CH4= 3H2+C2H2 (At 1000C K= 1.2 x 10^-3, Delta(H)= positive)
2CH4= H2 + C2H6 (At 1000C K= 4.2 x 10^-3, Delta (H)= positive)
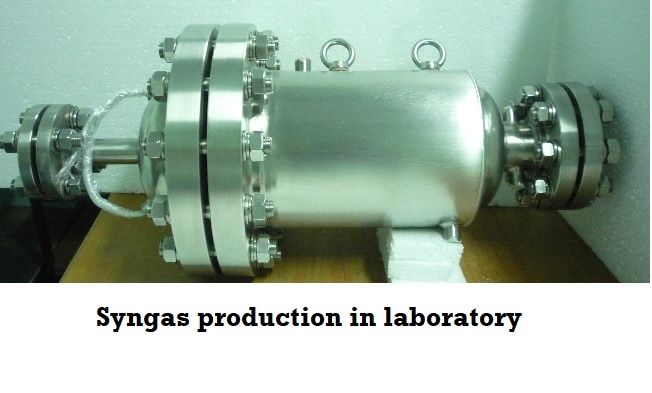
MHI is the source of syngas production. For laboratory KW and Commercial MW power.
Heat Methane and CO2
Fuel cells, High-velocity drying, and Surface-heating, including simulation. The diagram below relates to iron ore reduction without catalysts, with some carbon monoxide or hydrogen reduction. Contact MHI for nozzles supplied.
Catalytic Bed Heating/ See also Fluidized Bed. See also Quasi-R(R). Airtorch® units can have a high-temperature input and may be supplied with high-pressure shells/schedules. Various types of supplemental heating can be included. MHI specializes in custom units. Please be aware that customization adds a considerable degree of cost. Use also for aseptic and antimicrobial processing.
Chronology of Steel Developments Direct Reduction/Hybrid Systems.
Packaging, Sealing, Chemical Reactions, Cracking and Hot CO2 or CO reactions
Drying is best done with hot air or hot steam. This prevents the toxic use of drying salts (chemicals) and reduces sulfuric and hydrochloric acid emissions. In one application the return on expenditure was very high – the cost of the capital equipment was recovered in two years. When using salts or desiccants they have to be dried for reuse. Using salts could create a very high energy/material recovery cost.
The application of the Airtorch™ in Fluidized Beds! Please call MHI for details.
Airtorch® Applications are in Curing and Baking, Batteries, both electrical and thermal, Batch Heating, Electrochemical and Chemical Processing, Drying and cooking, difficult core drying exhaust gas heating, Curing, Dehumidification, Dehydrating, Film Drying, Finishing Systems, Food Processing, Fruit Ripening, Heat Battery, Heat Recovery Supplement, Heat Treating, Crucible or Hopper Heating, Dyes, and Ink Drying, Testing, Make-up Air Heating, Metal Finishing, Reheating, Roasting (peanuts, groundnuts, pecans, nuts, coffee, corn, soya, Semi-Conductor Manufacturing, Disinfection, Sterilizing, Standby Heating, Textile Drying, Varnish Drying, Rod and Wire Manufacturing, Spacecraft Aircraft And Aircraft Stands and Manufacturing, Air Curtains, Air Drying, Annealing, Enhanced Booster Heating, Motor Winding Burn off, Paint Baking/Drying, Pharmaceutical Manufacturing, Plastic Curing, Preheating, Ore processing.
Aluminum Brazing | Scorching/Burn off/Curing |
The Airtorch® has opened up new possibilities in the brazing and joining technologies. Whereas brazing furnaces were cumbersome and expensive in the past, Airtorch® allows for inexpensive processes.![]() | The Airtorch® can be used for curing, surface burning, and sealing operations. The possibilities are endless, as Air, Nitrogen, Helium, and Argon can be used.![]() |
Large Die Heating | Direct Ceramic Drying |
The Airtorch® allows large die heat-up reclaim energy with low flash. | The Airtorch® can achieve very high temperatures without contamination. Therefore, direct drying is a natural application. Free and bonded water can be easily removed. MHI also manufactures several Airtorch® Continuous ovens.![]() |
Binder Burn Off | Heating for Tensile Testing |
Easy, uniform, safe, and collectible binder burn-off. Substantially improve quality and productivity for ceramics, nitrides, powder metals, etc.![]() | When high temperatures are needed in spaces where resistance heating elements cannot be used, the Airtorch® provides the solution. |
Packaging or Sealing | Die Heating |
Designed for long life and high temperatures, the non-contaminating Airtorch® is an ideal solution for inline packaging or sealing processes.![]() | Use the Airtorch® adie preheating devices in the metal forging and rolling industries.![]() |
Soldering, Melting, and Dental | |
Use the Airtorch® for softenen solder, and melt of precious metals and glass. Use for rapid glazing, burnout, and quick melts. This feature applies to the dental, jewelry, and glass industries. |
Nozzle Heating | Gas Preheating |
The glass industry uses the high-temperature Airtorch® to enable uniform flow and reflow of molten glass. The air temperature can be as high as 1200°C with a meager flow rate.![]() | Airtorch® can rapidly heat various atmospheres: Air, Nitrogen, Argon, Helium, etc. Call MHI for more information. |
Microprocessor Heating | Light Fiber Processing |
Unique heating from 500°C to 1000°C. The Airtorch® produces laser-like hints to small areas of 5mm in diameter with stable and accurate control. | Uniformly free carbon from woven fibers with true convection. The Airtorch® creates hot, turbulent air that passes through the substrate for uniform and accurate heating. As carbon is released, the natural flow of clean, hot air flushes the airborne carbon away from the part and up the chimney.![]() |
Effective Heat Treating | Preheating for Welding |
Uniform rapid heating. The Airtorch® offers uniform high temperature and heats uniformly parts rapidly. It is very effective for metals when increasing hardness.![]() | With high accuracy and temperatures, the Airtorch® reduces the guesswork of preheating for welding applications. Offers accurate temperature read-out. |
Spot Decarborinzing (reducing hardness) | Ultimate UtiliOver-carbonizing |
ing causes hardness above most machining capabilities. The Airtorch® offers locatable, accurate, rapid heat-up cool-down to diffuse carbon allowing the metal’s tempering efficiently.![]() | Develop your application. The Airtorch® is capable of many applications where accuracy, uniformity, power, and high temperatures are required. Also benefit from whisper-like operations, energy efficiency, and ease of use.![]() ![]() |
Decarbonize the melting of tin, zinc, and aluminum with the Airtorch products. In a tin melting plant, it became costly to get new gas lines. The plant is considering melting with low-pressure drop Airtorches. It hopes to recover its expenditure in two years because of the enormous energy benefits of melting with an electric airtorch. MHI can assist with energy calculations.
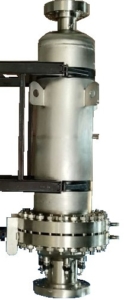
Airtorch Vert High-Pressure High Temperature
Are you looking for a very low-pressure drop high, efficient compact duct heater?
Convert to an electric oven with the highly compact SH duct heater module.
Extremely Compact High Power Duct Heater Airtorch®.
Energy efficiency is higher. Because of the controlled temperatures of an electric heater, they tend to be considerably more efficient than gas heaters.
1- 15 Kw 36 KW, 72kW , 144kW, 402 Kw, 900KW, 3 MW, 4 MW (PV)
Other MHI products like OAB® and Cascade e-ion may also be used for such applications.
Combustion and Scorching/Burn off/Curing
Arrhenius equation and influence of Temperature. Airtorch® can be used for curing, surface burning, sealing, and simulation operations. The possibilities are endless, as Air, Nitrogen, Helium, and Argon can be used. During combustion, the time for 98% combustion can change by several orders of magnitude for a 100°K rise in air temperature.
Scorching/burn-off/curing
Conversion for N2 | Weight, Nitrogen | Volume, Nitrogen | ||
Pounds (lb) | kilograms (kg) | Cubic feet (SCF) | Cubic meters (Nm3) | |
1 pound | 1.0 | 0.454 | 13.80 | 0.363 |
————— | ————– | —————- | ————- | ————— |
1 kilogram | 2.205 | 1.0 | 30.42 | 0.7996 |
1 SCF gas | 0.07245 | 0.03286 | 1.0 | 0.02628 |
1 Nm3 gas | 2.757 | 1.2506 | 38.04 | 1.0 |
SCF (Standard cubic foot) gas was measured at 1 atmosphere and 70°F. Nm3 (Normal cubic meter) gas was measured at 1 atmosphere and 0°C. |
44.01 kg is the mass of one kilo-mole of CO2
14.0067 kg is the mass of one kilo-mole of N2
The average molar mass of dry air is 28.97 kg/kilo-mole.
Easy Design and Selection
Choose KW, MW, and even MW/m2 flux
If the flow is higher than 40 SCFM, please choose from MVTA models
If the temperature required is above 1150°C, please choose PDF models
If the flow rate needed is of the order of 2-40 SCFM, please select from MTA, VTA, or LTA models or MVTA925 for flanged units
- DPF – Up to 1150°C-1250°C/~2200°F. DPF models can take fan or blower input and a compressed air/gas input.
- Large Flow MVTA. For 1000-1100°C. These are sealed process gas heaters (THN or DNA class) with a blower or inline capability—high KW – High Flow.
- Large Flow GTA – For high-pressure vessel Airtorch® use. Custom engineering. Please contact us for assistance.
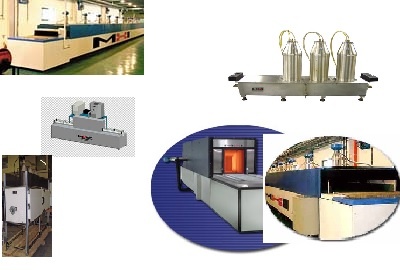
Continuous ovens with Airtorch® heating
CONVERSION TABLE OF MBtu/h to KW
MBtu/hour [MBtu/h] Kilowatt [kW]
0.01 MBtu/h 2.93 kW
0.1 MBtu/h 29.30 kW
1 MBtu/h 293.07 kW
2 MBtu/h 586.14 kW
3 MBtu/h 879.21 kW
5 MBtu/h 1465.35 kW
5.8 MBtu/h 1700 kW
8.54 MBtu/h 2500 KW
10 MBtu/h 2930.71 kW
Comfort Air Heating
The Airtorch® allows significant room heating and humidity provided by the Steam Generators.
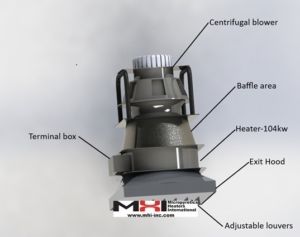
Comfort Airtorch®
Use efficient close to 100% efficient heating. Although there are competing technologies for low temperatures, like heat pumps, they do not work well when the outside temperature is less than 5C. Many people must use supplementary heating with gas or oil to keep warm. This, of course, is not carbon-friendly. Stay with the airtorch technologies for energy efficiency, decarbonization, and simplicity. For industrial heating, hydrogen does not compete unless the hydrogen is heated with Airtorch technologies.
The Airtorch® allows large die heat-up, including reclaiming dies and aluminum. Attempt the removal of inorganic and organic salts, fuel cells, general heat treatment for bending and de-flashing/deburring, drum heating, plastic rolls, welding organics like plastic soldering disinfection, drying, and rapid paper and pulp dry: combustion/flow simulation, curing, drying, or bonding of paper boards.
With a 4 kW machine, plan to dry 2-4 Kg/hr. of desiccant.
Click to see the Die Heating Applications Presentation |
Don’t hesitate to contact MHI for ROI calculations for typical Die Heating.